Lean Performance Improvement: A Guide
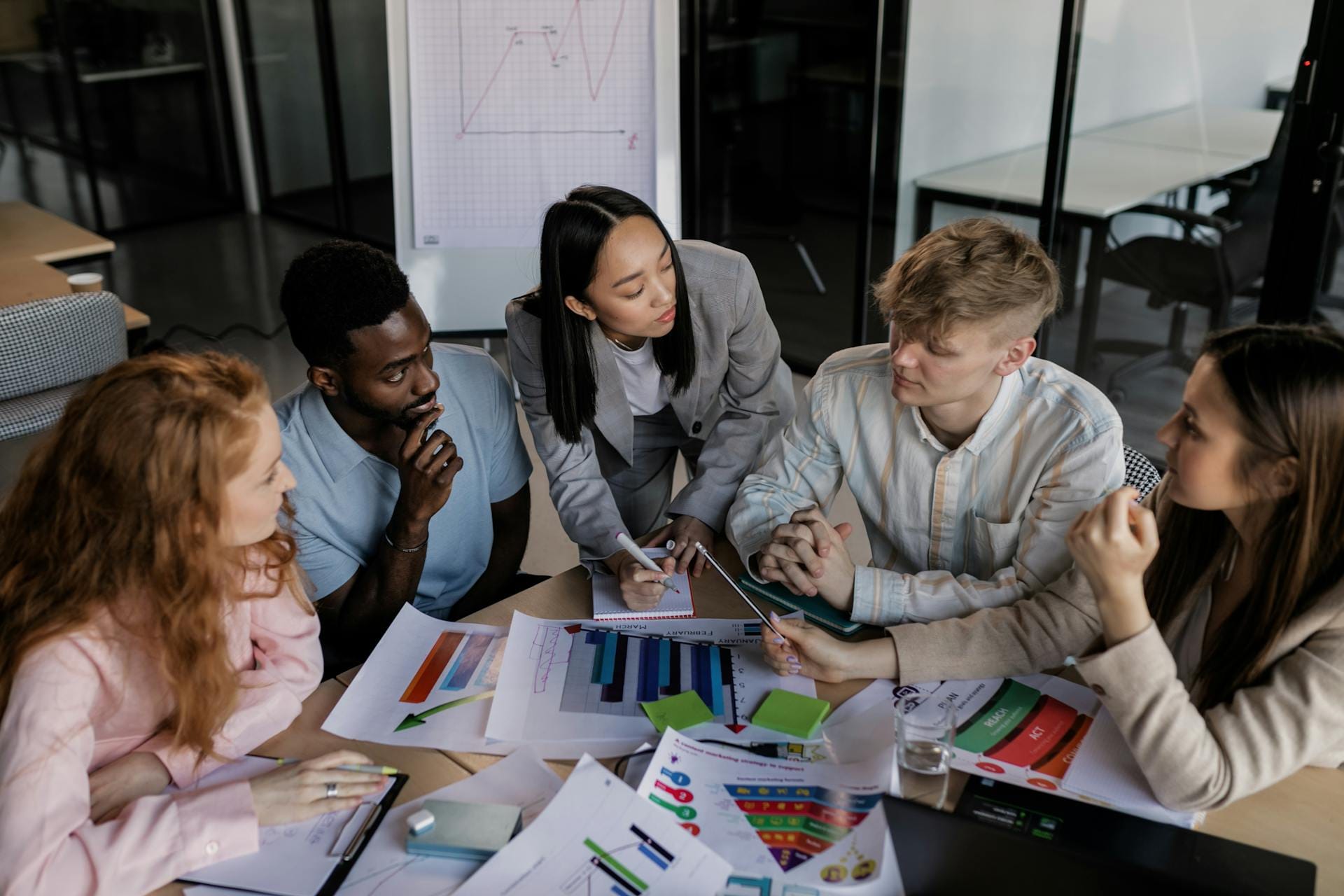
It seems unbelievable, but whenever you talk about Lean performance improvement methods, kanban, scrum and other similar process methodologies, the first thing that comes to people's minds is post-it notes glued together on a chalkboard.
Confusion aside, simplification and even trivialization of the lean performance improvement method requires that we re-install some of its history, its principles and objectives.
In this post, we intend to rescue, albeit briefly, some of the key concepts of Lean performance improvement.
The Lean Performance Improvement Method
Many still think of Toyota when it comes to Lean performance improvement. But nobody ever mentions MIT and professors James Womak and Daniel Jones, and their iconic book, "The Machine That Changed the World".
It's details such as these that make us think of the importance of keeping alive the original concepts of things, not to stifle thought and not evolve, but to avoid certain simplifications that lead to stereotyped behavior and decisions without foundation.
These two scholars have defined some concepts that we would like to discuss now, and which are the synthesis of the Lean performance improvement method.
Their focus is more on a change of mental model than on the use of visual tools and agile frameworks.
The 4 principles of Lean performance improvement
1- Focus on Value
The goal is to link enterprise value strategies with internal process modeling so you can be sure of your goals without straying off course.
For this, it's essential to determine the most appropriate metrics and KPIs, by monitoring processes constantly.
Consequently, the focus should be on the proper creation of processes, so that they manage the value determined in the organization's strategy.
2 - Process Guidance
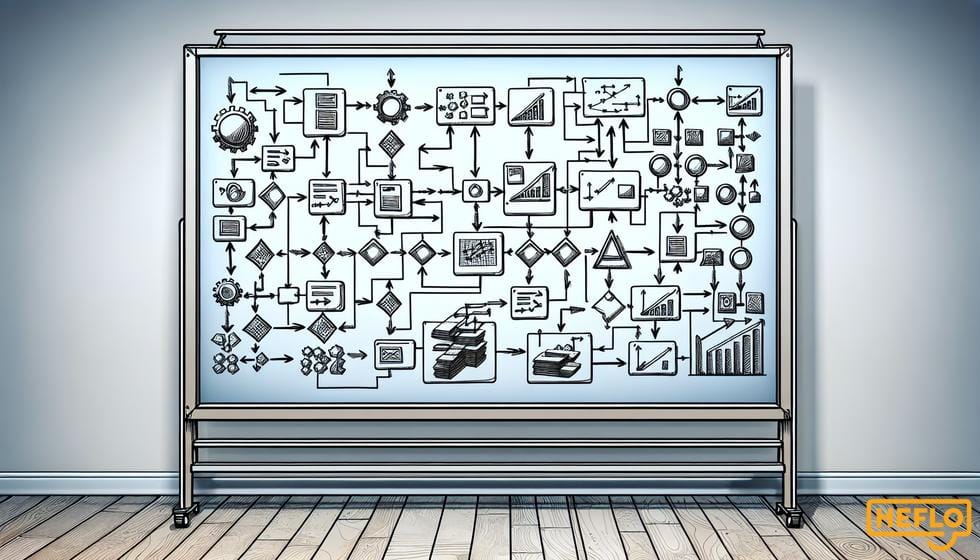
Another key aspect of the Lean performance improvement methodology is its focus on processes, but without taking an eye off the customer, of course!
The correct process is ultimately one that will deliver the value the customer wants.
The change in mentality that must be pursued is to leave behind management by objectives and instead pursue management by processes, which means:
- The mapping and visualization of all process flows
- Process standardization
- Disciplinary proceedings
- The process should only exist if demand exists for its output
- Value must flow in a single direction, without setbacks
- Each process delivery must comply with the expected level of quality, without wastage, delays and at the lowest possible cost
3- Teamwork
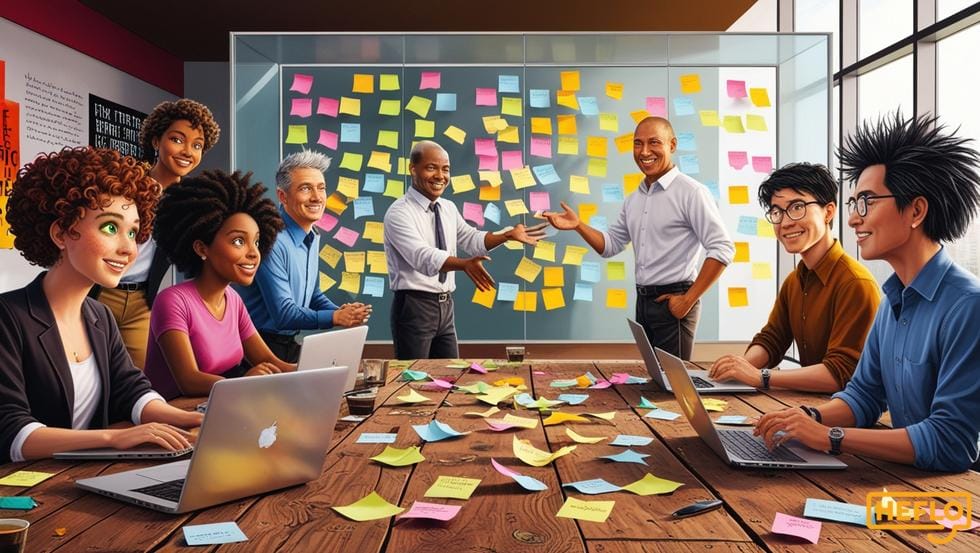
Complementary skills, the exchange of ideas, constant feedback, autonomy, "being your own boss", having multiple roles.
These are some of the qualities of a Lean team. This requires HR processes to also be tailored to search for professionals with this type of profile.
4- Continuous Improvement
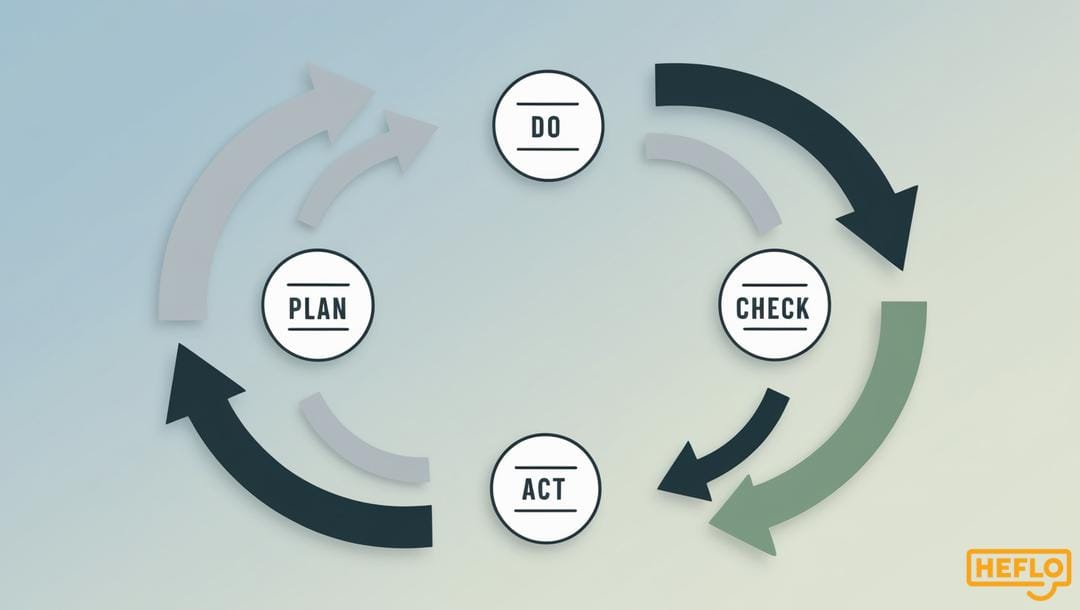
Excellence is the watchword and it can only be achieved with the constant modeling of processes in a search for continuous improvement.
In this context, the classic quest for process barriers should include the identification and dismantling of wastes such as the following:
- Excess inventory
- Low quality
- Rework
- Unnecessary movements and activities
- Wait times
- A lack of team motivation
Summarizing the principles of Lean performance improvement:
- Change from a functional system to an organization of processes
- Seek excellence on a daily basis
- Align operational actions with the company's strategic focus
- Create value through processes
- The appreciation of staff competencies and motivation
- Change the traditional hierarchical relationship to a "team spirit" focus
- Rapid adaptation power
- Process simplification
Does your company use or intend to use the Lean performance improvement method?
Be sure to look for an agile and intuitive BPM tool to make this mission even faster and more assured.