Exploring the Japanese Process Improvement Methodologies
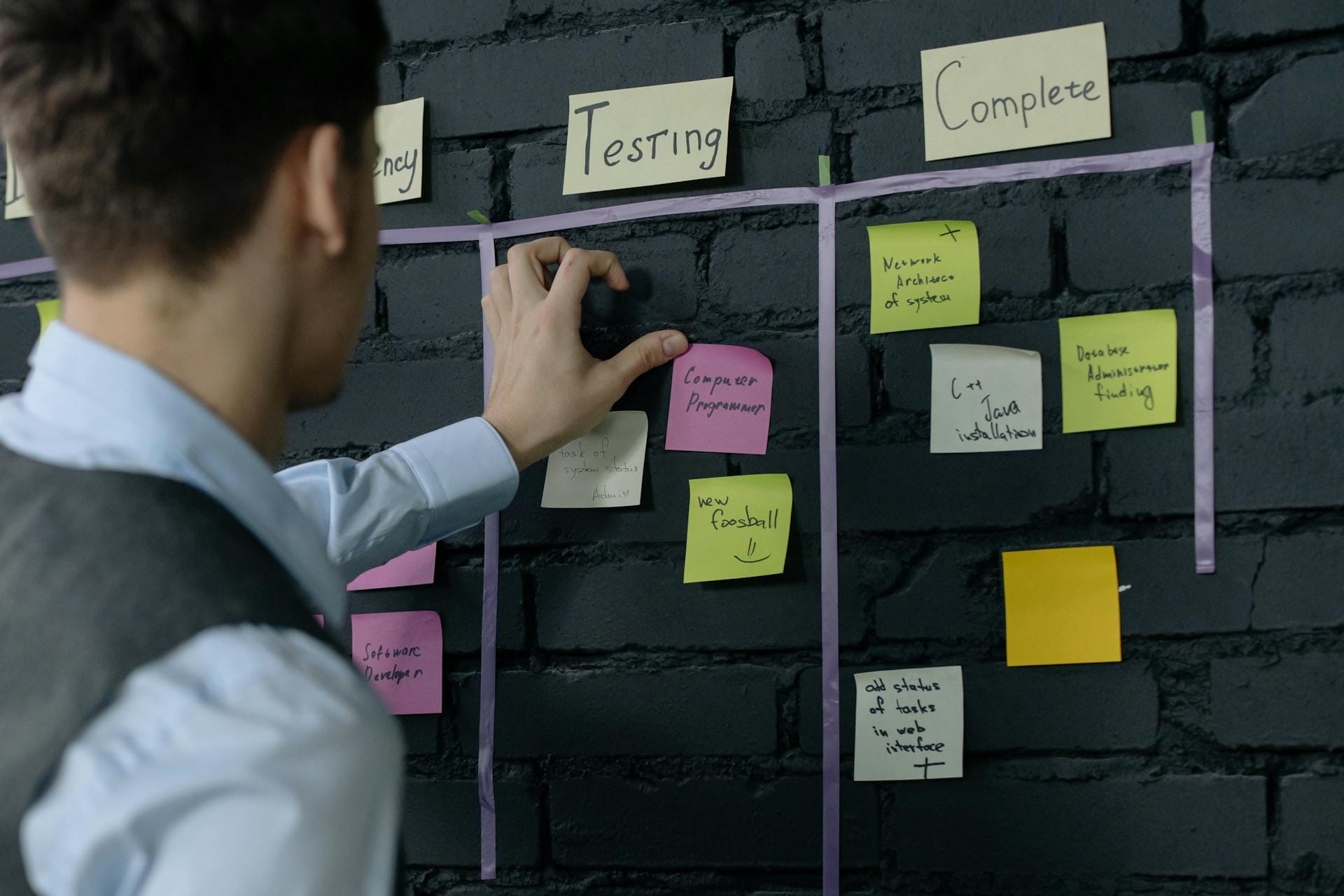
Unlocking efficiency is a critical goal for businesses worldwide, and the Japanese process improvement methodologies offer a treasure trove of strategies to achieve it. In this article, we delve into key concepts such as Kaizen, the 5S Methodology, Just-In-Time (JIT), Total Quality Management (TQM), and Lean Manufacturing.
You can expect a comprehensive exploration of these techniques, providing actionable insights to enhance productivity and streamline operations.
Kaizen: The Heart of Japanese Process Improvement
Kaizen, a Japanese term meaning "change for the better" or "continuous improvement," is a core principle in Japanese process improvement methodologies. Originating in Japan after World War II, Kaizen has become a fundamental aspect of various industries worldwide, particularly in manufacturing and business management.
Kaizen means improvement. Moreover, it means continuing improvement in personal life, home life, social life, and working life. When applied to the workplace, Kaizen means continuing improvement involving everyone - managers and workers alike. Masaaki Imai
At its essence, Kaizen focuses on small, incremental changes rather than large-scale transformations. This approach encourages employees at all levels to contribute ideas for improving processes, enhancing efficiency, and reducing waste. By fostering a culture of continuous improvement, organizations can achieve significant long-term benefits without the need for substantial investments or overhauls.
Principles of Kaizen
Kaizen is built on several key principles:
- Continuous Improvement: The belief that there is always room for improvement, no matter how small.
- Employee Involvement: Encouraging all employees to participate in the improvement process, leveraging their unique insights and experiences.
- Standardization: Establishing and maintaining standards to ensure consistent quality and performance.
- Elimination of Waste: Identifying and removing non-value-adding activities to streamline processes.
- Quality Control: Ensuring that improvements lead to higher quality outcomes.
Kaizen in Practice
Implementing Kaizen typically involves the following steps:
- Identify Opportunities: Recognize areas where improvements can be made.
- Analyze Processes: Examine current processes to understand their strengths and weaknesses.
- Develop Solutions: Generate ideas for improvement, often through brainstorming sessions.
- Implement Changes: Put the proposed solutions into action.
- Review Results: Assess the impact of the changes and make further adjustments as needed.
By adhering to these steps, organizations can create a cycle of continuous improvement that drives efficiency and productivity. Kaizen's emphasis on small, manageable changes makes it an accessible and effective strategy for businesses of all sizes and industries.
5S Methodology
The 5S Methodology is a cornerstone of Japanese process improvement techniques, designed to enhance efficiency and productivity in the workplace. Originating from lean manufacturing principles, the 5S Methodology focuses on creating a clean, organized, and efficient environment. The five pillars of this methodology are:
- Seiri (Sort): This step involves sorting through all items in a workspace and removing unnecessary ones. The goal is to keep only what is essential, thereby reducing clutter and making it easier to find important tools and materials.
- Seiton (Set in Order): Once the unnecessary items are removed, the next step is to organize the remaining items. Everything should have a designated place, and tools should be arranged in a manner that maximizes efficiency and minimizes wasted time.
- Seiso (Shine): This step emphasizes cleanliness. Regular cleaning schedules are established to ensure that the workspace remains tidy. A clean environment not only improves safety but also boosts morale and productivity.
- Seiketsu (Standardize): Standardization involves creating consistent procedures and practices for maintaining the first three S's. This could include checklists, schedules, and visual cues to ensure that the new level of organization is maintained.
- Shitsuke (Sustain): The final step is about sustaining the improvements over the long term. This requires ongoing training, audits, and a culture of continuous improvement to ensure that the 5S principles become ingrained in the organizational culture.
Implementing the 5S Methodology can significantly streamline business processes, making it an ideal approach for companies looking to scale repetitive and voluminous tasks. For those interested in further enhancing their business process management (BPM) strategies, tools like HEFLO can provide valuable support in documenting and automating these processes.
Just-In-Time (JIT)
Just-In-Time (JIT) is a cornerstone of the Japanese process improvement methodology, particularly within the framework of Lean manufacturing. Originating from the Toyota Production System (TPS), JIT focuses on reducing waste and improving efficiency by producing only what is needed, when it is needed, and in the amount needed.
The primary goal of JIT is to minimize inventory levels and reduce carrying costs. By synchronizing production schedules with demand, companies can significantly cut down on excess inventory, which often ties up capital and storage space. This approach not only enhances operational efficiency but also increases flexibility, allowing businesses to respond more swiftly to market changes.
Implementing JIT requires a high level of coordination and communication across the supply chain. Suppliers must be reliable and capable of delivering materials quickly and accurately. Additionally, production processes need to be streamlined to ensure that each step adds value and contributes to the final product without unnecessary delays.
One of the key benefits of JIT is the dramatic reduction in lead times. By eliminating bottlenecks and ensuring that resources are available exactly when needed, companies can accelerate their production cycles. This not only boosts productivity but also enhances product quality, as issues can be identified and addressed more promptly.
While JIT is most commonly associated with manufacturing, its principles can be applied to various business processes. For instance, in service industries, JIT can help streamline workflows, reduce waiting times, and improve customer satisfaction. By adopting JIT, organizations can achieve a more agile and responsive operational model, ultimately driving better business outcomes.
Total Quality Management (TQM)
Total Quality Management (TQM) is a comprehensive approach to long-term success through customer satisfaction. Originating in Japan, TQM integrates fundamental management techniques, existing improvement efforts, and technical tools under a disciplined approach focused on continuous improvement.
Quality is not an act, it is a habit. Aristotle
One of the key principles of TQM is the involvement of all employees. From top management to frontline workers, everyone is encouraged to contribute ideas and take ownership of their roles in the quality improvement process. This collective effort helps in identifying inefficiencies and implementing effective solutions.
Another critical aspect of TQM is the use of data-driven decision-making. By systematically collecting and analyzing data, organizations can pinpoint areas of improvement and measure the impact of changes. Tools such as statistical process control (SPC) and root cause analysis are commonly used to support this analytical approach.
Continuous improvement, or Kaizen, is a fundamental concept within TQM. It involves making small, incremental changes regularly to enhance processes and reduce waste. This ongoing effort helps organizations stay competitive and responsive to market demands.
Customer focus is also a central tenet of TQM. By understanding and meeting customer needs and expectations, organizations can build strong relationships and ensure long-term success. This customer-centric approach drives the development of high-quality products and services that stand out in the marketplace.
In summary, Total Quality Management is a holistic approach that integrates employee involvement, data-driven decision-making, continuous improvement, and customer focus to achieve excellence in all organizational processes. By adopting TQM principles, organizations can unlock efficiency and drive sustainable growth.
Lean Manufacturing
Lean Manufacturing is a systematic approach aimed at minimizing waste without sacrificing productivity. Originating from the Toyota Production System (TPS), Lean principles were popularized by James Womack and Daniel Jones in their seminal book, The Machine That Changed the World. The primary objective of Lean is to create more value for customers with fewer resources by optimizing the flow of work and eliminating inefficiencies.
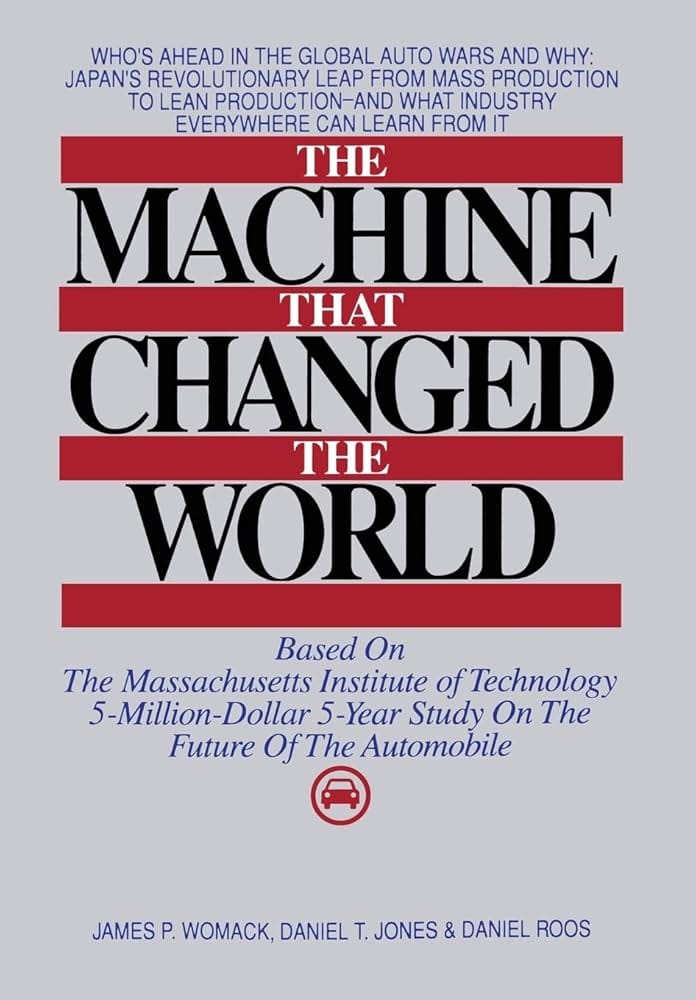
Lean Manufacturing employs a variety of tools and techniques to achieve its goals. One of the most prominent tools is Value Stream Mapping (VSM), which visualizes the entire production process, from raw materials to the delivery of the final product. By mapping out each step, organizations can identify and eliminate non-value-adding activities, thereby streamlining operations and reducing lead times.
Another critical aspect of Lean is the focus on the seven types of waste, often referred to as "Muda" in Japanese. These include:
- Overproduction: Producing more than what is needed or before it is needed.
- Waiting: Idle time when resources are not being used efficiently.
- Transport: Unnecessary movement of products or materials.
- Extra Processing: Performing more work or using more resources than necessary.
- Inventory: Excess products and materials not being processed.
- Motion: Unnecessary movements by people.
- Defects: Efforts caused by rework, scrap, and incorrect information.
Lean Manufacturing also emphasizes continuous improvement, or "Kaizen," which involves all employees from the CEO to the shop floor workers. This culture of continuous improvement encourages small, incremental changes that collectively lead to significant enhancements in efficiency and quality.
While Lean principles were initially developed for manufacturing, they have been successfully applied in various sectors, including services and transactional settings. The flexibility and adaptability of Lean tools make them valuable for any organization looking to improve efficiency and reduce waste.
In conclusion, the Japanese process improvement methodologies offer a robust framework for enhancing efficiency and productivity across various industries. By embracing principles such as Kaizen, Lean, and Just-In-Time, organizations can foster a culture of continuous improvement, reduce waste, and optimize their operations. As businesses worldwide seek to remain competitive in an ever-evolving market, adopting these time-tested Japanese process improvement techniques can be a transformative step towards achieving sustainable success and operational excellence.