Business process modeling for dummies: 7 tips and ideas
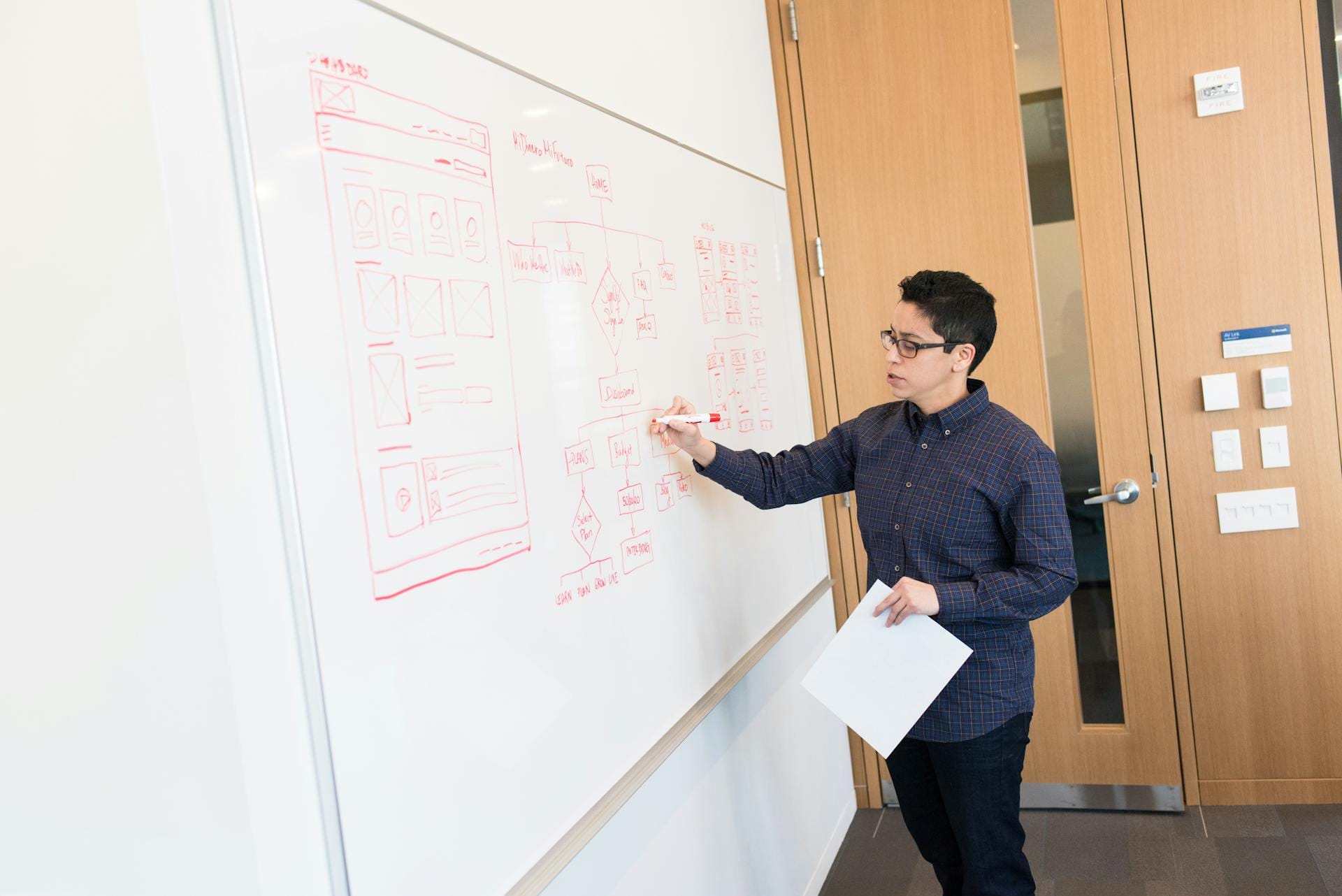
Process modeling is a way to create a visual map of how a series of activities or tasks are carried out in a business setting.
Imagine drawing a diagram that shows every step taken to complete a job, from start to finish. This diagram includes all the tasks, decision points, and the flow of work that happens.
By laying everything out visually, it becomes much easier to see where improvements can be made. For example, if a process has any unnecessary steps or bottlenecks, they become obvious. It also helps everyone involved in a project understand exactly how things are supposed to work, which makes it easier to communicate and implement changes.
In short, process modeling helps businesses see their workflows clearly, so they can improve efficiency and achieve their goals more effectively.
Before we dive into our tips, let's watch this introductory class on BPMN, the premier modeling notation for describing business processes.
Concepts of business process modeling for dummies
Adding value to the customer and the business
Before we talk about the process chain, the activities that comprise it, and how to make it more efficient and productive, reducing bottlenecks, delays, and wastes (among other possible measures for continuous process improvement), we need to understand the concept of the value-added production chain.
Think of it this way: When delivering a product or service to an end customer, the consumer pays the price for it, in cash, based on the value that the solution gives them. Or rather, their perception of the value of that solution.
It could be a pot, a trip, a car, a physiotherapy session, software; it's not important: a problem was solved for the client, a wish or desire was met, and that is worth something to the consumer. So much so, that they are willing to pay for it.
On the other hand, the company performs a series of tasks and activities to deliver this product or service to the customer. It plans, buys, stocks, transforms, paints, joins, budgets, delegates, cuts, packs, delivers etc.
Each of these tasks individually has a cost, and the sum of all of them will define a total cost. This sum should be less than the amount the customer is willing to pay for the product or service that he or she wants. Otherwise, there would be no profit, wouldn't you agree?
Ready: This is the value-added concept (for laymen) along with a chain of productive processes: it must be greater in the customer's perception than how much it cost the company.
In fact, the more efficiently a company can create this perception of value in a product or service for its customers, spending as little as possible, the more valuable the company itself will be considered, and the more value will have been added to the business, for example).
Process chain, processes, and activities
This business process modeling for dummies description should already be helping you to understand the concept.
Even so, some simple BPM definitions for dummies can always help more:
Process: A set of interrelated activities carried out in chronological order (some in parallel) to carry out a job that has the objective of meeting the needs of someone or an organization. Eg: The process of delivering a good.
Activity: Tasks or jobs performed by people or software through specific resources. Eg: The activity of filing the invoice ticket for delivered goods.
Productive chain, process chain or value chain: Every process that is interrelated for the final delivery of value (service or product) from an organization to an end customer: Eg: The process chain of an e-commerce site involves several processes, among them, the delivery of the merchandise.
With all of this in mind, process modeling, even for lay people, begins to become clearer: How can we make this productive chain present the lowest possible cost and deliver the perceived average value?
This is what we'll look at next.
Business process modeling for dummies and continuous improvement
Continuous improvement is a BPM technique used to ensure that processes are always being performed in the most efficient way possible, i.e., by using fewer resources and delivering more value to the next process.
There are several ways to analyze this and design a new, improved and optimized process, but as this is business process modeling for dummies, let's present 3 simple examples to understand:
- Bottlenecks: A bottleneck is a time during a process where all previous activities will be paralyzed if the current process is not functioning properly or efficiently. For example, a restaurant is obtaining orders, has enough seats, the kitchen and all other activities are working efficiently, except for the delivery of the orders to the tables, because a waiter is missing.
- Delays: Following the example of the restaurant, an oven located in an inappropriate place is causing more time to be taken to prepare food. All the tasks that depend on it are delayed.
- Waste: The improper use of refrigerators is leading to excessive energy expenditure and the expiration of some foods.Thus, continuous improvement methods analyze these processes and activities to find ways to avoid bottlenecks, delays, and waste.
To do this, new processes are designed with the help of BPM tools, using an internationally recognized notation, BPMN 2.0, creating process flows that are easy to understand and efficient to perform.