Explorer les méthodologies japonaises d'amélioration des processus métier
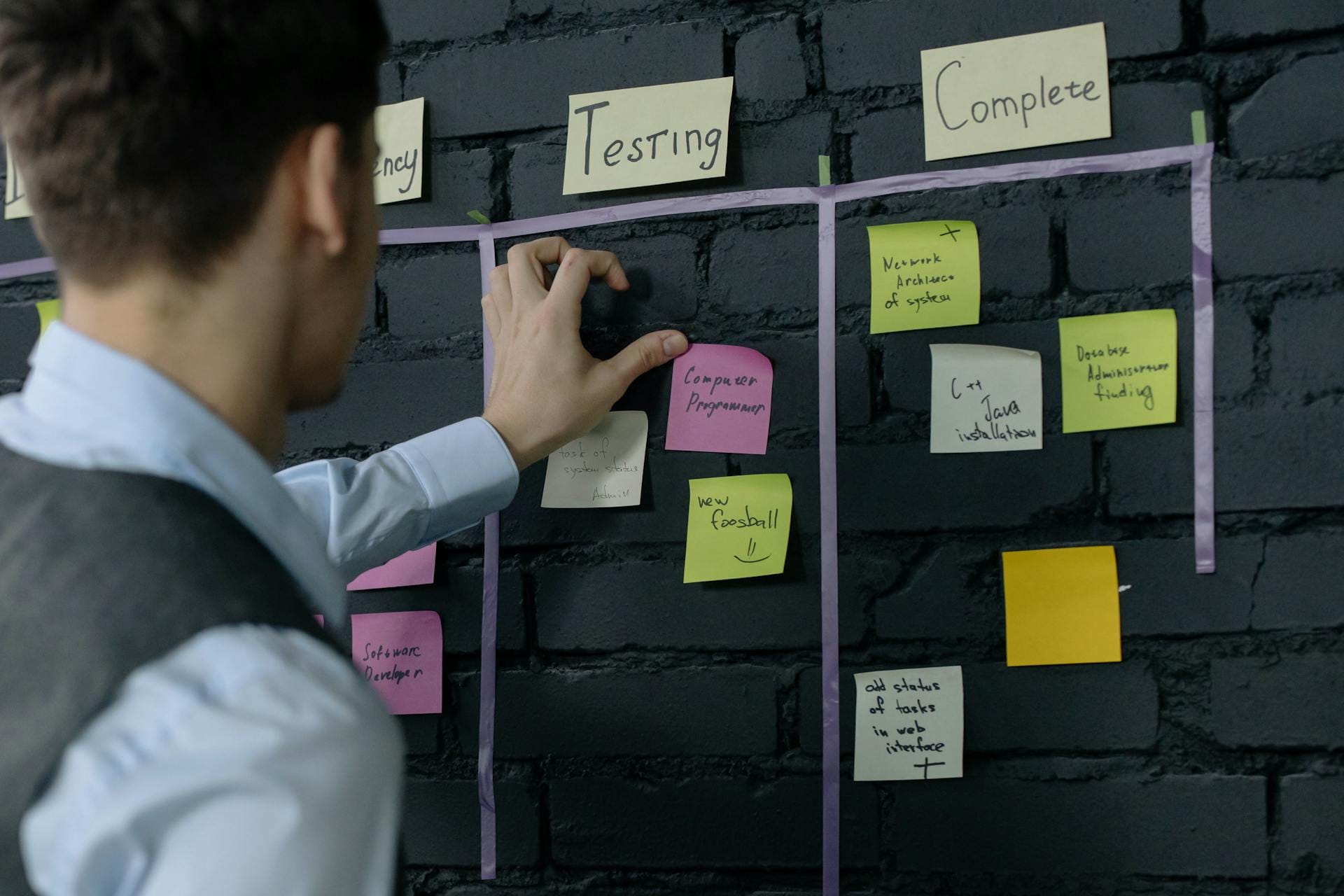
Libérer l'efficacité est un objectif crucial pour les entreprises du monde entier, et les méthodologies japonaises d'amélioration des processus offrent une mine de stratégies pour y parvenir. Dans cet article, nous explorons des concepts clés tels que Kaizen, la Méthodologie 5S, le Just-In-Time (JIT), la Gestion de la Qualité Totale (TQM) et la Fabrication Lean. Vous pouvez vous attendre à une exploration complète de ces techniques, fournissant des idées concrètes pour améliorer la productivité et rationaliser les opérations.
Kaizen : Le Cœur de l'Amélioration des Processus Japonais
Kaizen, un terme japonais signifiant "changement pour le mieux" ou "amélioration continue", est un principe fondamental dans les méthodologies d'amélioration des processus japonais. Originaire du Japon après la Seconde Guerre mondiale, Kaizen est devenu un aspect fondamental de diverses industries dans le monde entier, en particulier dans la fabrication et la gestion des affaires.
Kaizen signifie amélioration. De plus, cela signifie une amélioration continue dans la vie personnelle, la vie à la maison, la vie sociale et la vie professionnelle. Lorsqu'il est appliqué au lieu de travail, Kaizen signifie une amélioration continue impliquant tout le monde - les managers et les travailleurs. Masaaki Imai
À son essence, Kaizen se concentre sur de petits changements incrémentaux plutôt que sur des transformations à grande échelle. Cette approche encourage les employés à tous les niveaux à contribuer des idées pour améliorer les processus, augmenter l'efficacité et réduire les déchets. En favorisant une culture d'amélioration continue, les organisations peuvent obtenir des avantages significatifs à long terme sans avoir besoin d'investissements substantiels ou de révisions majeures.
Principes de Kaizen
Kaizen repose sur plusieurs principes clés :
- Amélioration Continue : La croyance qu'il y a toujours une marge d'amélioration, aussi petite soit-elle.
- Implication des Employés : Encourager tous les employés à participer au processus d'amélioration, en tirant parti de leurs perspectives et expériences uniques.
- Standardisation : Établir et maintenir des normes pour garantir une qualité et des performances constantes.
- Élimination des Déchets : Identifier et supprimer les activités n'apportant pas de valeur ajoutée pour rationaliser les processus.
- Contrôle de la Qualité : S'assurer que les améliorations conduisent à des résultats de meilleure qualité.
Kaizen en Pratique
La mise en œuvre de Kaizen implique généralement les étapes suivantes :
- Identifier les Opportunités : Reconnaître les domaines où des améliorations peuvent être apportées.
- Analyser les Processus : Examiner les processus actuels pour comprendre leurs forces et leurs faiblesses.
- Développer des Solutions : Générer des idées d'amélioration, souvent par le biais de séances de brainstorming.
- Mettre en Œuvre les Changements : Mettre en action les solutions proposées.
- Revoir les Résultats : Évaluer l'impact des changements et apporter des ajustements supplémentaires si nécessaire.
En adhérant à ces étapes, les organisations peuvent créer un cycle d'amélioration continue qui stimule l'efficacité et la productivité. L'accent mis par Kaizen sur de petits changements gérables en fait une stratégie accessible et efficace pour les entreprises de toutes tailles et de tous secteurs.
Méthodologie 5S
La méthodologie 5S est une pierre angulaire des techniques japonaises d'amélioration des processus, conçue pour améliorer l'efficacité et la productivité sur le lieu de travail. Issue des principes de la fabrication lean, la méthodologie 5S se concentre sur la création d'un environnement propre, organisé et efficace. Les cinq piliers de cette méthodologie sont :
- Seiri (Trier) : Cette étape consiste à trier tous les éléments d'un espace de travail et à éliminer ceux qui sont inutiles. L'objectif est de ne conserver que l'essentiel, réduisant ainsi l'encombrement et facilitant la recherche des outils et matériaux importants.
- Seiton (Ranger) : Une fois les éléments inutiles éliminés, l'étape suivante consiste à organiser les éléments restants. Tout doit avoir une place désignée, et les outils doivent être disposés de manière à maximiser l'efficacité et à minimiser le temps perdu.
- Seiso (Nettoyer) : Cette étape met l'accent sur la propreté. Des calendriers de nettoyage réguliers sont établis pour garantir que l'espace de travail reste propre. Un environnement propre améliore non seulement la sécurité, mais aussi le moral et la productivité.
- Seiketsu (Standardiser) : La standardisation implique la création de procédures et de pratiques cohérentes pour maintenir les trois premiers S. Cela peut inclure des listes de contrôle, des calendriers et des repères visuels pour garantir que le nouveau niveau d'organisation soit maintenu.
- Shitsuke (Soutenir) : La dernière étape consiste à soutenir les améliorations sur le long terme. Cela nécessite une formation continue, des audits et une culture d'amélioration continue pour s'assurer que les principes 5S deviennent ancrés dans la culture organisationnelle.
La mise en œuvre de la méthodologie 5S peut considérablement rationaliser les processus métier, en faisant une approche idéale pour les entreprises cherchant à optimiser des tâches répétitives et volumineuses. Pour ceux qui souhaitent améliorer davantage leurs stratégies de gestion des processus métier (BPM), des outils comme HEFLO peuvent fournir un soutien précieux dans la documentation et l'automatisation de ces processus.
Just-In-Time (JIT)
Just-In-Time (JIT) est une pierre angulaire de la méthodologie d'amélioration des processus japonais, en particulier dans le cadre de la fabrication Lean. Originaire du système de production Toyota (TPS), le JIT se concentre sur la réduction des déchets et l'amélioration de l'efficacité en produisant uniquement ce qui est nécessaire, quand cela est nécessaire, et en quantité nécessaire.
L'objectif principal du JIT est de minimiser les niveaux de stock et de réduire les coûts de stockage. En synchronisant les calendriers de production avec la demande, les entreprises peuvent réduire considérablement les excès de stock, qui immobilisent souvent du capital et de l'espace de stockage. Cette approche améliore non seulement l'efficacité opérationnelle, mais augmente également la flexibilité, permettant aux entreprises de répondre plus rapidement aux changements du marché.
La mise en œuvre du JIT nécessite un haut niveau de coordination et de communication tout au long de la chaîne d'approvisionnement. Les fournisseurs doivent être fiables et capables de livrer les matériaux rapidement et avec précision. De plus, les processus de production doivent être rationalisés pour garantir que chaque étape ajoute de la valeur et contribue au produit final sans retards inutiles.
L'un des principaux avantages du JIT est la réduction spectaculaire des délais de livraison. En éliminant les goulets d'étranglement et en s'assurant que les ressources sont disponibles exactement au moment où elles sont nécessaires, les entreprises peuvent accélérer leurs cycles de production. Cela augmente non seulement la productivité, mais améliore également la qualité des produits, car les problèmes peuvent être identifiés et résolus plus rapidement.
Bien que le JIT soit le plus souvent associé à la fabrication, ses principes peuvent être appliqués à divers processus métier. Par exemple, dans les industries de services, le JIT peut aider à rationaliser les flux de travail, réduire les temps d'attente et améliorer la satisfaction des clients. En adoptant le JIT, les organisations peuvent atteindre un modèle opérationnel plus agile et réactif, ce qui conduit finalement à de meilleurs résultats commerciaux.
Gestion de la Qualité Totale (TQM)
La Gestion de la Qualité Totale (TQM) est une approche globale visant le succès à long terme par la satisfaction du client. Originaire du Japon, le TQM intègre des techniques de gestion fondamentales, des efforts d'amélioration existants et des outils techniques sous une approche disciplinée axée sur l'amélioration continue.
La qualité n'est pas un acte, c'est une habitude. Aristote
Un des principes clés du TQM est l'implication de tous les employés. De la haute direction aux travailleurs de première ligne, chacun est encouragé à proposer des idées et à assumer la responsabilité de son rôle dans le processus d'amélioration de la qualité. Cet effort collectif aide à identifier les inefficacités et à mettre en œuvre des solutions efficaces.
Un autre aspect critique du TQM est l'utilisation de la prise de décision basée sur les données. En collectant et en analysant systématiquement les données, les organisations peuvent identifier les domaines d'amélioration et mesurer l'impact des changements. Des outils tels que le contrôle statistique des processus (SPC) et l'analyse des causes profondes sont couramment utilisés pour soutenir cette approche analytique.
L'amélioration continue, ou Kaizen, est un concept fondamental du TQM. Elle consiste à apporter régulièrement de petits changements incrémentaux pour améliorer les processus et réduire les déchets. Cet effort continu aide les organisations à rester compétitives et réactives aux demandes du marché.
La focalisation sur le client est également un principe central du TQM. En comprenant et en répondant aux besoins et attentes des clients, les organisations peuvent établir des relations solides et assurer un succès à long terme. Cette approche centrée sur le client stimule le développement de produits et services de haute qualité qui se démarquent sur le marché.
En résumé, la Gestion de la Qualité Totale est une approche holistique qui intègre l'implication des employés, la prise de décision basée sur les données, l'amélioration continue et la focalisation sur le client pour atteindre l'excellence dans tous les processus organisationnels. En adoptant les principes du TQM, les organisations peuvent débloquer l'efficacité et stimuler une croissance durable.
Lean Manufacturing
Lean Manufacturing est une approche systématique visant à minimiser les déchets sans sacrifier la productivité. Originaire du Toyota Production System (TPS), les principes Lean ont été popularisés par James Womack et Daniel Jones dans leur livre séminal, The Machine That Changed the World. L'objectif principal du Lean est de créer plus de valeur pour les clients avec moins de ressources en optimisant le flux de travail et en éliminant les inefficacités.
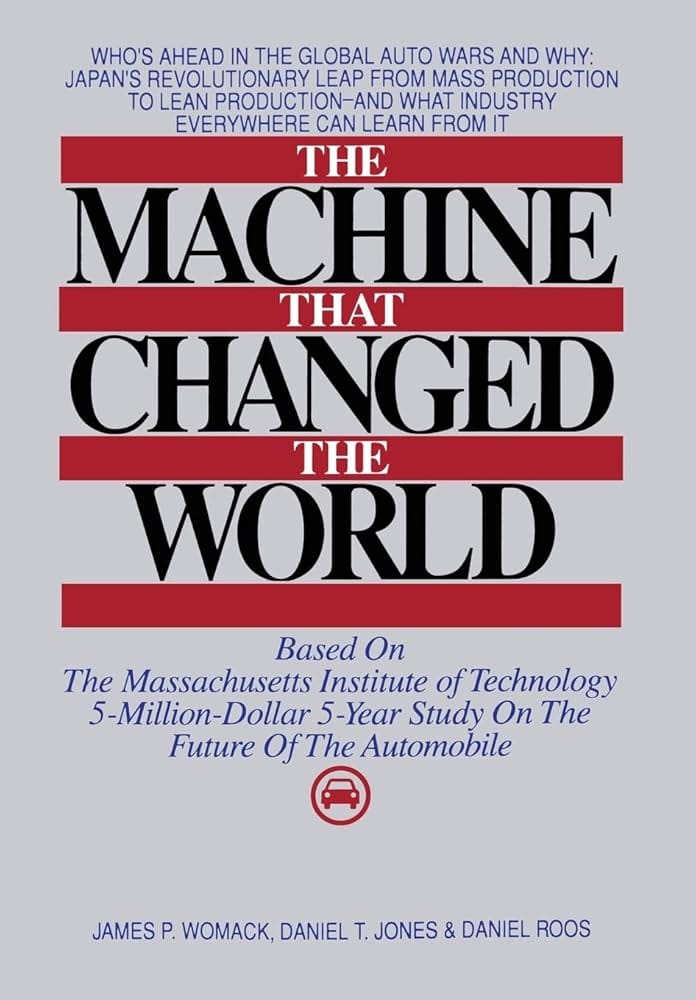
Lean Manufacturing utilise une variété d'outils et de techniques pour atteindre ses objectifs. L'un des outils les plus importants est la cartographie de la chaîne de valeur (VSM), qui visualise l'ensemble du processus de production, des matières premières à la livraison du produit final. En cartographiant chaque étape, les organisations peuvent identifier et éliminer les activités sans valeur ajoutée, rationalisant ainsi les opérations et réduisant les délais de livraison.
Un autre aspect critique du Lean est l'accent mis sur les sept types de déchets, souvent appelés "Muda" en japonais. Ceux-ci incluent :
- Surproduction : Produire plus que ce qui est nécessaire ou avant que ce soit nécessaire.
- Attente : Temps d'inactivité lorsque les ressources ne sont pas utilisées efficacement.
- Transport : Mouvement inutile de produits ou de matériaux.
- Traitement supplémentaire : Effectuer plus de travail ou utiliser plus de ressources que nécessaire.
- Inventaire : Produits et matériaux excédentaires non traités.
- Mouvement : Mouvements inutiles des personnes.
- Défauts : Efforts causés par la retouche, les rebuts et les informations incorrectes.
Lean Manufacturing met également l'accent sur l'amélioration continue, ou "Kaizen", qui implique tous les employés, du PDG aux ouvriers de l'atelier. Cette culture d'amélioration continue encourage de petits changements incrémentaux qui, collectivement, conduisent à des améliorations significatives de l'efficacité et de la qualité.
Bien que les principes Lean aient été initialement développés pour la fabrication, ils ont été appliqués avec succès dans divers secteurs, y compris les services et les environnements transactionnels. La flexibilité et l'adaptabilité des outils Lean les rendent précieux pour toute organisation cherchant à améliorer l'efficacité et à réduire les déchets.
En conclusion, les méthodologies japonaises d'amélioration des processus offrent un cadre solide pour améliorer l'efficacité et la productivité dans divers secteurs. En adoptant des principes tels que Kaizen, Lean et Just-In-Time, les organisations peuvent favoriser une culture d'amélioration continue, réduire les déchets et optimiser leurs opérations. Alors que les entreprises du monde entier cherchent à rester compétitives dans un marché en constante évolution, l'adoption de ces techniques japonaises éprouvées d'amélioration des processus peut être une étape transformative vers la réussite durable et l'excellence opérationnelle.