An In-Depth Look at Total Quality Management (TQM)
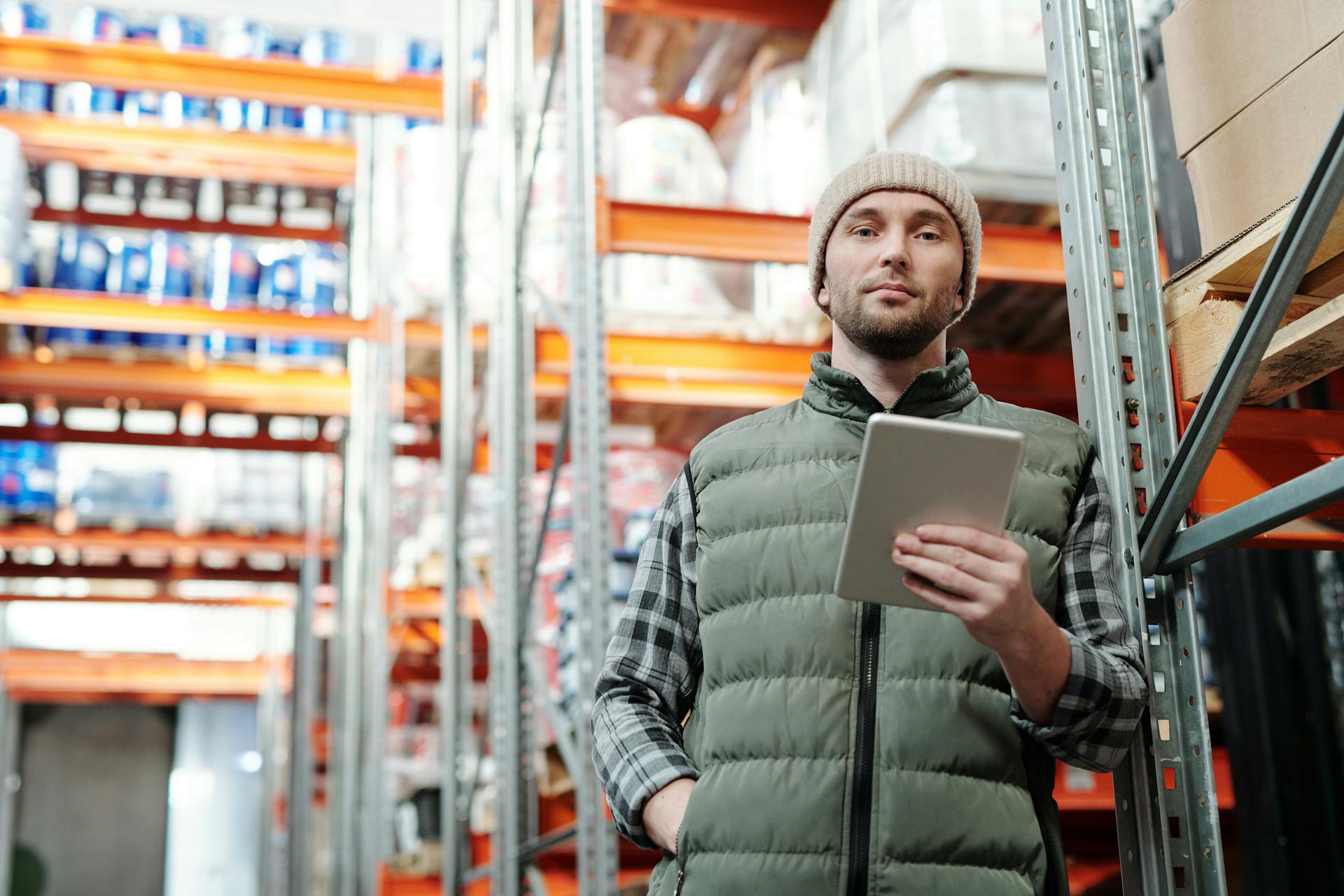
Total Quality Management (TQM) is a comprehensive approach to improving the quality of products and services through continuous refinements in response to continuous feedback. It is a management philosophy that seeks to integrate all organizational functions to focus on meeting customer needs and organizational objectives.
History and Evolution of TQM
The journey of Total Quality Management (TQM) is a fascinating exploration of how quality control and management practices have evolved over time. From its early beginnings to its current state, TQM has undergone significant transformations, influenced by various industrial needs and technological advancements.
Early Beginnings
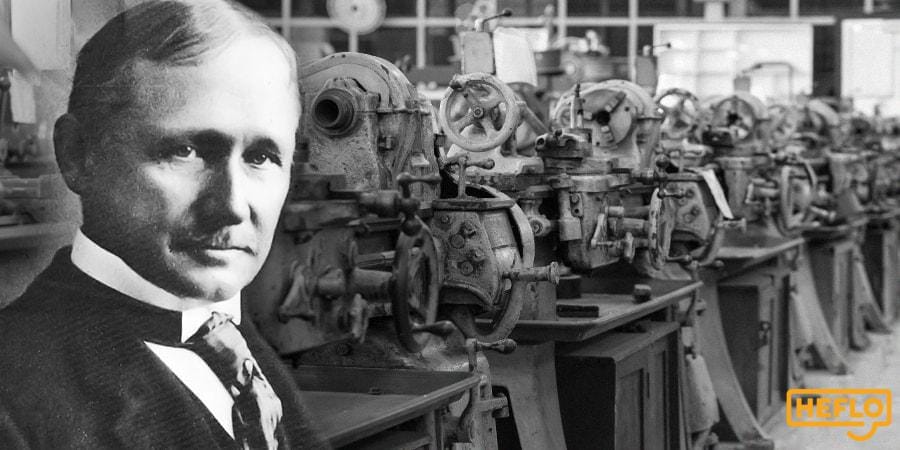
The roots of TQM can be traced back to the early 20th century with the advent of the Industrial Revolution. During this period, the focus was primarily on increasing production efficiency. Quality control was rudimentary, often limited to the final inspection of products. Frederick Taylor's principles of scientific management laid the groundwork for systematic approaches to improving efficiency and productivity.
The Influence of World War II
World War II marked a significant turning point in the history of quality management. The need for high-quality military equipment led to the development of more sophisticated quality control techniques. The United States and other Allied nations began to adopt statistical quality control methods, pioneered by Walter Shewhart and further developed by W. Edwards Deming and Joseph Juran. These methods emphasized the importance of process control and continuous improvement.
Post-War Developments
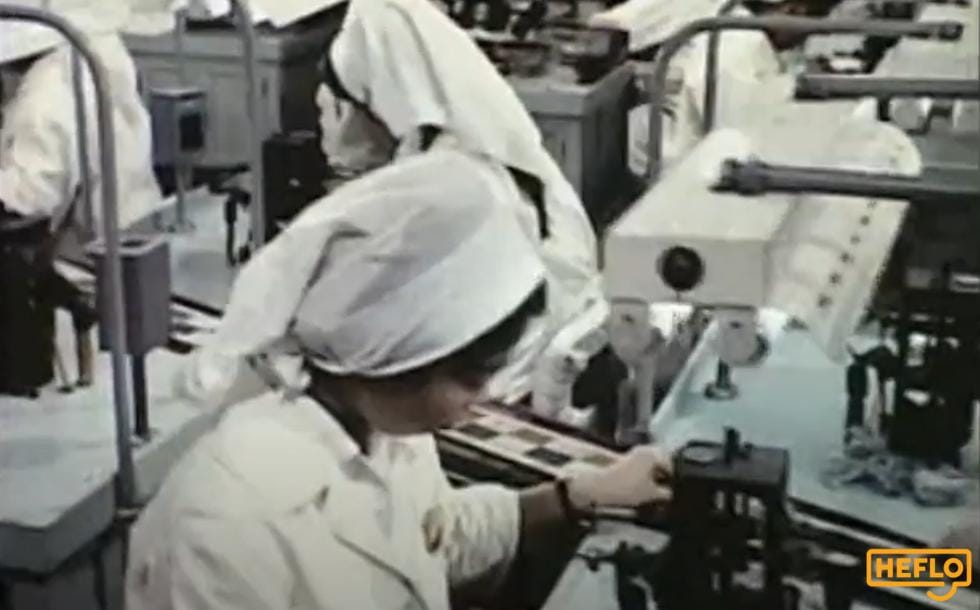
After the war, Japanese industries embraced the teachings of Deming and Juran, leading to a quality revolution in Japan. The Japanese approach to quality management, known as Total Quality Control (TQC), focused on involving all employees in the quality improvement process. This holistic approach laid the foundation for what would later become TQM.
The Rise of TQM in the West
By the 1980s, Western companies began to recognize the success of Japanese firms and started to adopt TQM principles. The emphasis shifted from merely inspecting finished products to improving processes and preventing defects. Key concepts such as customer focus, continuous improvement, and employee involvement became central to TQM.
Core Principles of TQM
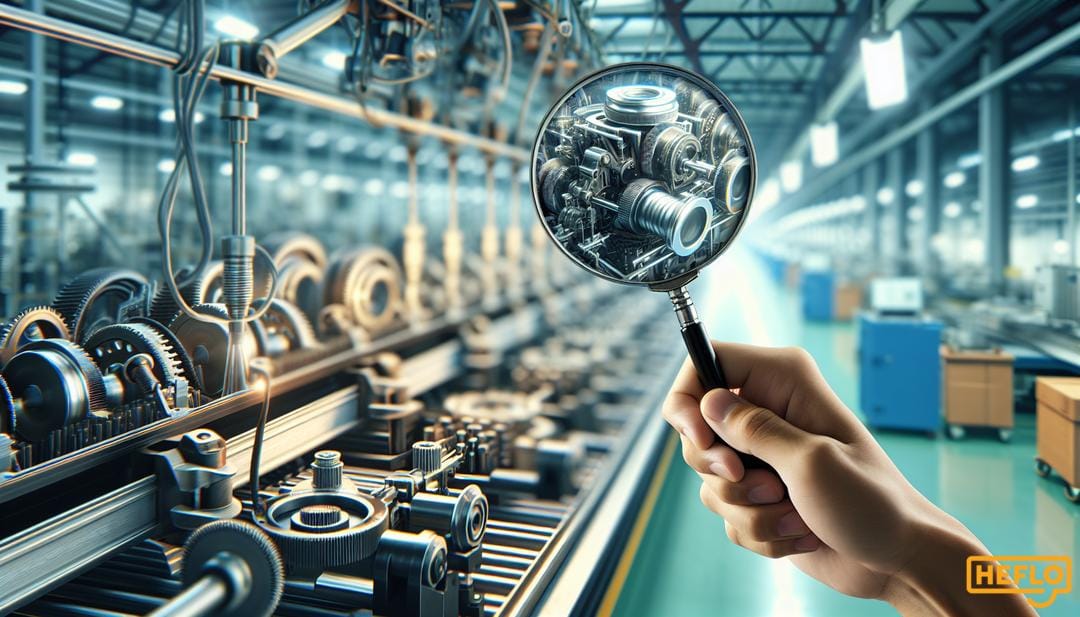
Total Quality Management (TQM) is a comprehensive approach aimed at improving the quality of products and services through continuous refinements in response to continuous feedback. Understanding its core principles can help organizations achieve higher efficiency and customer satisfaction.
Quality in a service or product is not what you put into it. It is what the client or customer gets out of it. - Peter Drucker
Customer Focus
At the heart of TQM is the principle of customer focus. Organizations must understand and meet the needs and expectations of their customers. This involves gathering customer feedback, analyzing it, and using it to drive improvements in products and services.
Leadership Commitment
Effective leadership is essential for TQM. Leaders must establish a clear vision, set goals, and create an environment that encourages quality improvement. They should also lead by example, demonstrating their commitment to quality in every aspect of their work.
Employee Involvement
All employees should be involved in the quality improvement process. This can be achieved through training, empowerment, and creating a culture where employees feel valued and motivated to contribute to quality initiatives.
Process Approach
TQM emphasizes the importance of understanding and managing processes. By focusing on processes, organizations can identify inefficiencies and areas for improvement, leading to more consistent and predictable outcomes.
Integrated System
An integrated system ensures that all aspects of the organization work together towards common goals. This involves aligning processes, policies, and objectives across departments to create a cohesive and efficient operation.
Continuous Improvement
Continuous improvement is a fundamental principle of TQM. Organizations should constantly seek ways to improve their processes, products, and services. This can be achieved through regular reviews, feedback loops, and the implementation of incremental changes.
Data-Driven Decision Making
Decisions should be based on data and analysis rather than intuition or guesswork. By using accurate and relevant data, organizations can make more informed decisions that lead to better outcomes.
Mutually Beneficial Supplier Relationships
Building strong relationships with suppliers is crucial for TQM. Organizations should work closely with their suppliers to ensure that materials and services meet quality standards, fostering a collaborative approach to quality improvement.
TQM Tools and Techniques
Understanding the various tools and techniques associated with Total Quality Management (TQM) can significantly enhance the efficiency and effectiveness of organizational processes. These tools and techniques are designed to identify, analyze, and improve quality-related issues, ensuring that products and services meet or exceed customer expectations.
Seven Basic Quality Tools
1. Cause-and-Effect Diagram (Ishikawa or Fishbone Diagram)
This tool helps identify, explore, and display the possible causes of a specific problem or quality characteristic. It is particularly useful in brainstorming sessions to uncover root causes.
2. Check Sheet
A structured, prepared form for collecting and analyzing data. It is a simple and effective way to gather data in real-time at the location where the data is generated.
3. Control Chart
Used to study how a process changes over time. Data are plotted in time order, and control charts always have a central line for the average, an upper line for the upper control limit, and a lower line for the lower control limit.
4. Histogram
A graphical representation of the distribution of numerical data. It provides an estimate of the probability distribution of a continuous variable and helps in understanding the underlying frequency distribution.
5. Pareto Chart
A bar graph that shows which factors are more significant. It is based on the Pareto Principle, which states that roughly 80% of problems come from 20% of causes.
6. Scatter Diagram
Used to determine the relationship between two variables. It helps in identifying potential root causes of problems by showing correlations between variables.
7. Flowchart
A visual representation of the steps in a process. Flowcharts are used to understand and communicate how a process works, identify bottlenecks, and find areas for improvement.
Advanced Quality Tools
1. Failure Mode and Effects Analysis (FMEA)
A systematic method for evaluating processes to identify where and how they might fail and assessing the relative impact of different failures to identify the parts of the process that are most in need of change.
2. Statistical Process Control (SPC)
Uses statistical methods to monitor and control a process. This helps ensure that the process operates efficiently, producing more specification-conforming products with less waste.
3. Design of Experiments (DOE)
A systematic method to determine the relationship between factors affecting a process and the output of that process. It is used to find cause-and-effect relationships and optimize processes.
Implementation of TQM
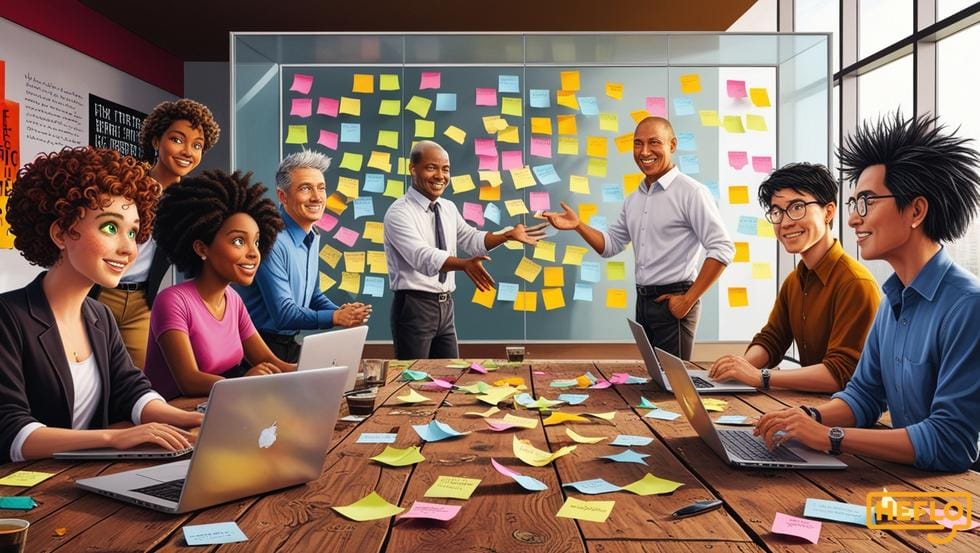
Implementing Total Quality Management (TQM) involves a comprehensive approach that integrates all organizational functions to focus on meeting customer needs and organizational objectives. This process requires a cultural shift within the organization, emphasizing continuous improvement, employee involvement, and a customer-centric approach.
Steps to Implement TQM
1. Commitment from Leadership
Successful TQM implementation begins with a strong commitment from top management. Leaders must demonstrate their dedication to quality by setting clear goals, providing necessary resources, and fostering an environment that encourages quality improvement.
2. Employee Involvement
Engaging employees at all levels is crucial for TQM. This can be achieved through training programs, quality circles, and open communication channels. Employees should be empowered to identify problems and suggest improvements.
3. Customer Focus
Understanding and meeting customer needs is at the heart of TQM. Organizations should gather customer feedback regularly and use it to drive improvements in products and services. This ensures that the organization remains aligned with customer expectations.
4. Process Management
Effective process management involves mapping out key processes, identifying areas for improvement, and implementing changes to enhance efficiency and quality. Tools such as process flowcharts and control charts can be useful in this stage.
5. Continuous Improvement
TQM is an ongoing process that requires a commitment to continuous improvement. Techniques such as Plan-Do-Check-Act (PDCA) cycles and Six Sigma can help organizations systematically improve their processes and products.
Using Technology in TQM
1. Data Analytics
Data analytics can play a significant role in TQM by providing insights into process performance and customer satisfaction. Analyzing data helps organizations identify trends, pinpoint issues, and make informed decisions.
2. Artificial Intelligence
Artificial Intelligence (AI) can enhance TQM by automating routine tasks, predicting quality issues, and providing real-time insights. For example, AI algorithms can analyze production data to detect anomalies and suggest corrective actions before defects occur.
3. Quality Management Software
Implementing quality management software can streamline TQM processes by providing tools for document control, audit management, and corrective action tracking. These systems help ensure that quality standards are consistently met and maintained.
Challenges in TQM Implementation
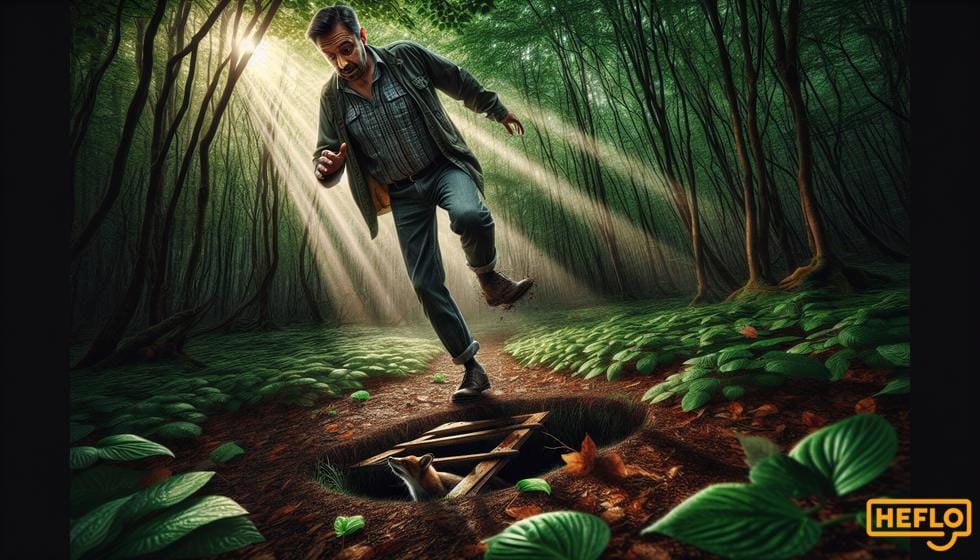
Implementing Total Quality Management (TQM) can be a transformative journey for organizations aiming to enhance their operational efficiency and customer satisfaction. However, the path to successful TQM implementation is often fraught with challenges that can hinder progress and dilute the intended benefits.
Resistance to Change
One of the most significant challenges in TQM implementation is resistance to change. Employees and management may be accustomed to existing processes and may view new quality management practices as disruptive. Overcoming this resistance requires effective communication, training, and a clear demonstration of the benefits of TQM.
Discover how to overcome change resistance and drive success! Watch our video to learn practical strategies for navigating and minimizing resistance to change.
Lack of Management Commitment
For TQM to be successful, it requires unwavering commitment from top management. Without their support, initiatives may lack the necessary resources and authority to drive meaningful change. Management must lead by example and actively participate in TQM activities to foster a culture of quality.
Inadequate Training
Proper training is essential for employees to understand and implement TQM principles effectively. Inadequate training can lead to misunderstandings and improper application of quality management techniques. Organizations must invest in comprehensive training programs to equip their workforce with the necessary skills and knowledge.
Insufficient Resources
Implementing TQM often requires significant resources, including time, money, and personnel. Organizations may struggle to allocate these resources, especially if they are already operating under tight budgets. Strategic planning and resource allocation are crucial to overcoming this challenge.
Poor Communication
Effective communication is vital for the successful implementation of TQM. Poor communication can lead to confusion, misalignment, and a lack of coordination among different departments. Establishing clear communication channels and regular updates can help mitigate this issue.
Integration with Existing Processes
Integrating TQM with existing business processes can be complex and challenging. Organizations must ensure that new quality management practices align with their current workflows and do not disrupt ongoing operations. Using tools like HEFLO can aid in documenting and automating business processes, making integration smoother.
Watch this video to understand why it is important to automate business processes and learn how to transform your organization for maximum efficiency. Don't miss out – your path to better business starts here!
Measuring and Monitoring Progress
Another challenge is the continuous measurement and monitoring of TQM initiatives. Organizations need to establish clear metrics and key performance indicators (KPIs) to track progress and identify areas for improvement. Regular audits and reviews can help maintain the momentum of TQM efforts.
Case Studies and Examples
Exploring real-world applications and success stories can provide valuable insights into how companies have effectively implemented Total Quality Management (TQM) to enhance their operations. By examining these case studies and examples, businesses can learn practical strategies and best practices to improve their own processes.
Case Study: Toyota's Lean Manufacturing
Toyota is often cited as a prime example of successful TQM implementation. The company adopted lean manufacturing principles, which focus on minimizing waste and maximizing efficiency. This approach has allowed Toyota to produce high-quality vehicles while reducing costs and improving customer satisfaction. Key elements of Toyota's TQM strategy include continuous improvement (Kaizen), just-in-time production, and employee involvement.
Continuous Improvement (Kaizen)
Kaizen, or continuous improvement, is a core component of Toyota's TQM approach. Employees at all levels are encouraged to identify areas for improvement and suggest solutions. This culture of continuous improvement has led to incremental changes that collectively result in significant enhancements in quality and efficiency.
Just-in-Time Production
Just-in-time (JIT) production is another critical aspect of Toyota's TQM strategy. By producing only what is needed, when it is needed, and in the amount needed, Toyota minimizes inventory costs and reduces waste. This approach requires precise coordination and a high level of quality control to ensure that each component meets the required standards.
Case Study: Motorola's Six Sigma
Motorola is another company that has successfully implemented TQM through its Six Sigma program. Six Sigma is a data-driven methodology aimed at reducing defects and improving process quality. Motorola's commitment to Six Sigma has resulted in significant cost savings and quality improvements across its operations.
Data-Driven Decision Making
Six Sigma relies heavily on data analysis to identify root causes of defects and variability in processes. By using statistical tools and techniques, Motorola can make informed decisions that lead to more consistent and reliable outcomes.
Employee Training and Certification
Motorola invests in extensive training and certification programs for its employees to ensure they have the skills and knowledge needed to implement Six Sigma effectively. This focus on education and development has been crucial to the company's success in achieving high levels of quality.
For companies looking to document and automate their business processes, tools like HEFLO can be invaluable in supporting TQM initiatives.
Future Trends in TQM
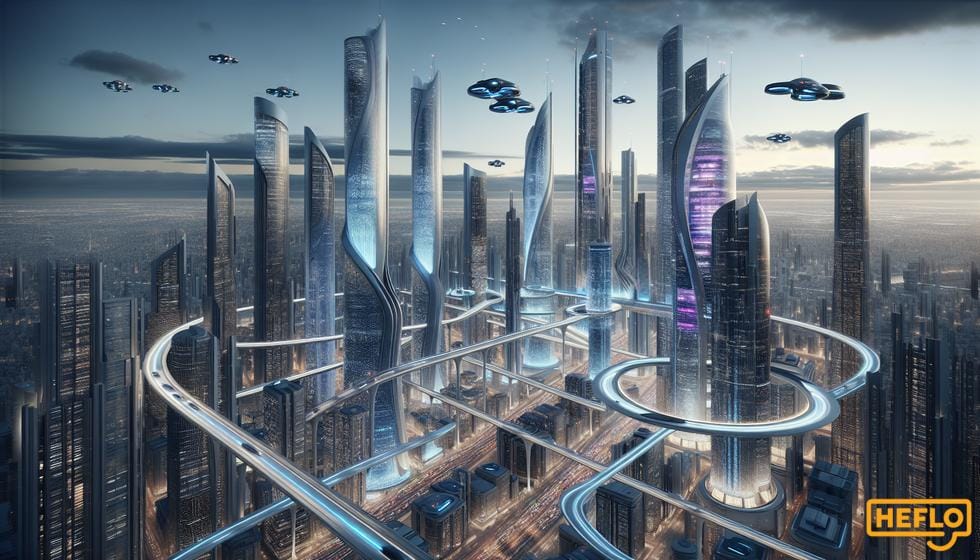
As organizations continue to evolve in a rapidly changing business environment, the principles and practices of Total Quality Management (TQM) are also undergoing significant transformations. These future trends are shaping how companies approach quality management, ensuring they remain competitive and efficient in their operations.
Integration of Digital Technologies
The integration of digital technologies is revolutionizing TQM. Advanced tools such as the Internet of Things (IoT), big data analytics, and cloud computing are enabling real-time monitoring and analysis of quality metrics. These technologies provide deeper insights into production processes, helping organizations to identify and rectify issues more swiftly and accurately.
Artificial Intelligence and Machine Learning
Artificial Intelligence (AI) and Machine Learning (ML) are becoming integral to TQM. These technologies can predict potential quality issues before they occur, optimize production processes, and enhance decision-making. For instance, AI-driven predictive maintenance can foresee equipment failures, reducing downtime and maintaining consistent quality standards.
Emphasis on Sustainability
There is a growing emphasis on sustainability within TQM practices. Companies are increasingly focusing on reducing waste, improving energy efficiency, and adopting eco-friendly materials. Sustainable quality management not only meets regulatory requirements but also appeals to environmentally conscious consumers, enhancing brand reputation.
Customer-Centric Approaches
Future trends in TQM are placing a stronger emphasis on customer-centric approaches. Understanding and exceeding customer expectations is becoming a primary focus. This involves leveraging customer feedback, conducting regular satisfaction surveys, and using data analytics to tailor products and services to meet customer needs more effectively.
Agile Quality Management
Agility in quality management is another emerging trend. Agile methodologies, originally developed for software development, are being adapted for TQM. This approach promotes flexibility, continuous improvement, and rapid response to changes, ensuring that quality management processes are more dynamic and responsive to market demands.
Enhanced Training and Development
Investing in the training and development of employees is becoming increasingly important. Future TQM trends emphasize the need for continuous learning and skill enhancement. Organizations are adopting e-learning platforms, virtual reality (VR) training, and other innovative methods to ensure their workforce is well-equipped to maintain high-quality standards.
In conclusion, Total Quality Management (TQM) stands as a comprehensive and strategic approach to organizational management that emphasizes continuous improvement, customer satisfaction, and the active involvement of all employees. By integrating TQM principles into their operations, organizations can achieve higher levels of efficiency, quality, and competitiveness. The holistic nature of TQM ensures that quality is not just a departmental concern but a core value that permeates every aspect of the business. As industries continue to evolve, the principles of Total Quality Management remain relevant, offering a robust framework for achieving long-term success and excellence.