Quality Assurance vs Quality Control: What are the differences?
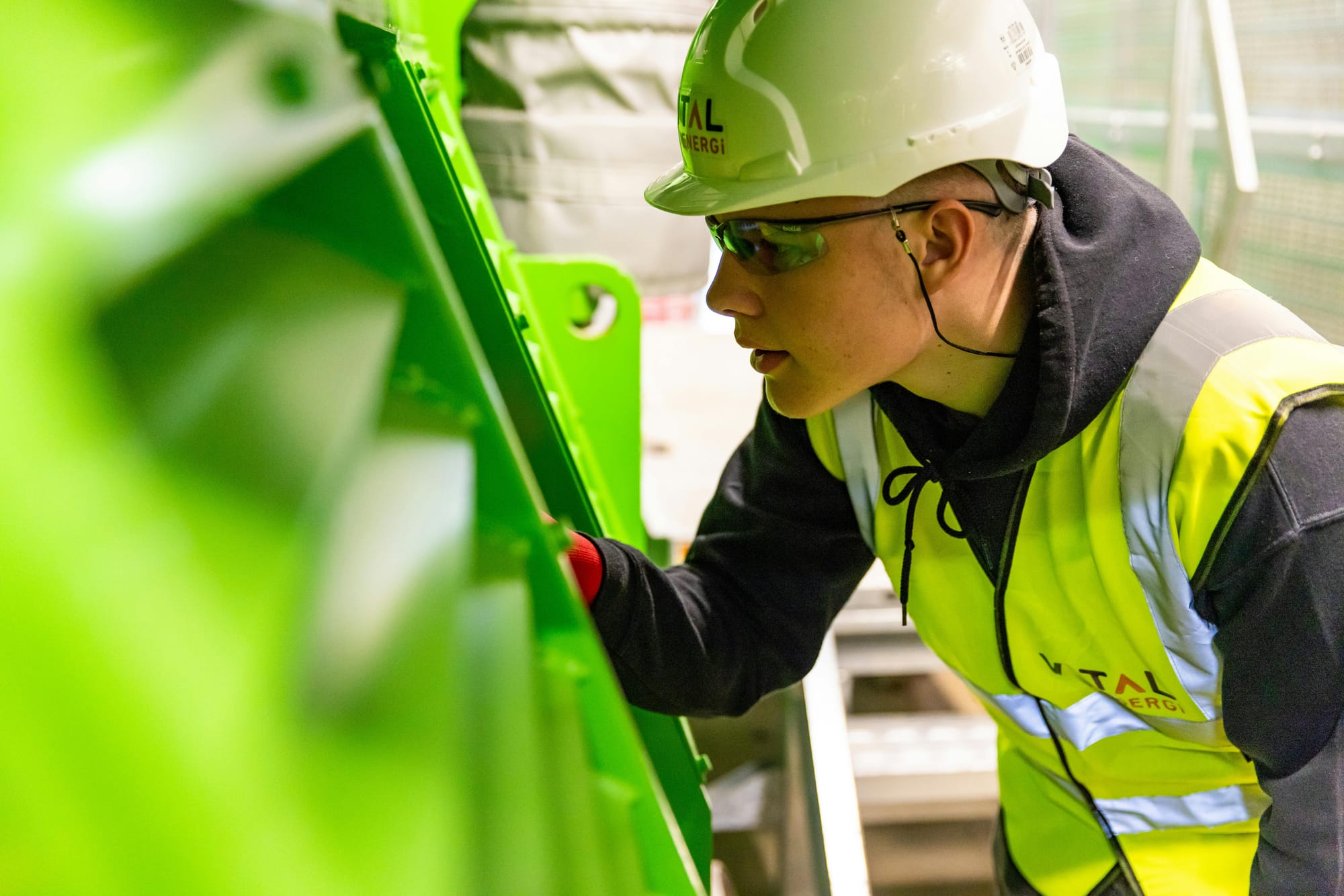
While Quality Assurance (QA) and Quality Control (QC) are sometimes used interchangeably, they represent distinct concepts and practices. Understanding the differences between QA and QC is crucial for companies aiming to scale repetitive and voluminous business processes effectively.
What is Quality Assurance?
Quality Assurance is a proactive process that focuses on preventing defects in the development and production stages. It involves the systematic planning and implementation of activities to ensure that quality requirements for a product or service will be fulfilled. QA is about building confidence that quality requirements will be met and is often integrated into the entire lifecycle of a product or service.
Key Aspects of Quality Assurance
- Process-Oriented: QA is concerned with improving and stabilizing production and associated processes to avoid or minimize issues that lead to defects.
- Preventive Action: The primary goal of QA is to prevent defects by focusing on the process used to make the product. It involves activities such as process checklists, process standards, and project audits.
- Continuous Improvement: QA involves continuous monitoring and improvement of processes through feedback loops and iterative enhancements.
What is Quality Control?
Quality Control, on the other hand, is a reactive process that focuses on identifying defects in the final products. QC involves the operational techniques and activities used to fulfill quality requirements. It is about verifying that the product meets the specified quality standards and is often performed at the end of the production process.
Key Aspects of Quality Control
- Product-Oriented: QC is concerned with identifying defects in the actual products produced. It involves activities such as inspection, testing, and reviewing.
- Corrective Action: The primary goal of QC is to identify defects after a product is developed and before it is released. It involves activities such as product testing and defect reporting.
- Compliance: QC ensures that the final product complies with the quality standards and requirements set by the company or regulatory bodies.
Summary of Differences
Aspect | Quality Assurance | Quality Control |
---|---|---|
Focus | Process-Oriented | Product-Oriented |
Goal | Prevent Defects | Identify Defects |
Timing | Proactive | Reactive |
Activities | Process Checklists, Standards, Audits | Inspection, Testing, Reviews |
Responsibility | Everyone Involved in the Process | Quality Control Team |
Conclusion
In summary, Quality Assurance and Quality Control are both critical components of a comprehensive quality management strategy. While QA focuses on preventing defects through process improvements, QC aims to identify and correct defects in the final product. By leveraging platforms like HEFLO, companies can effectively implement both QA and QC practices, ensuring that their products and services meet the highest quality standards.