What Is a Process Improvement Plan? A Complete Guide
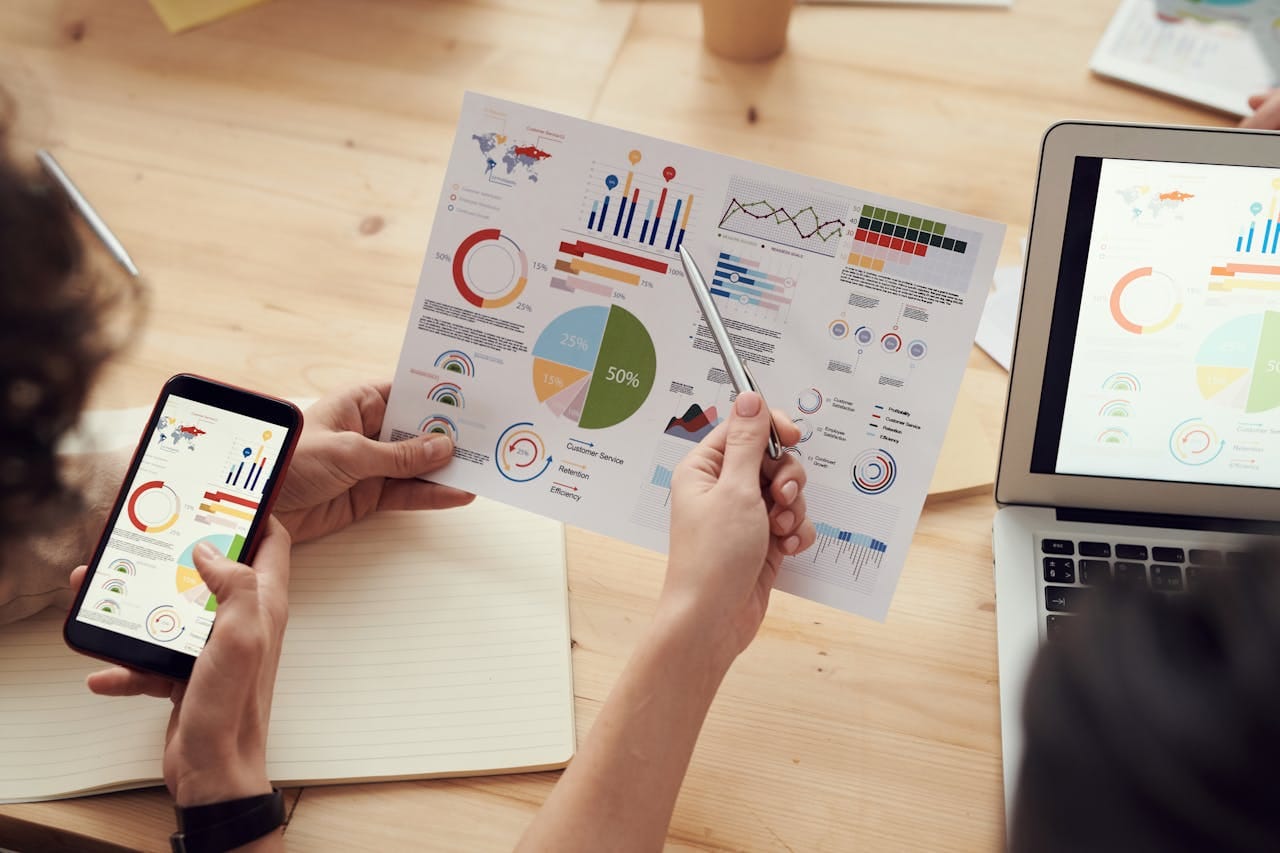
A process improvement plan functions as a strategic blueprint for systematically analyzing and enhancing core business processes. Whether the goal is optimizing resource allocation, accelerating throughput, or elevating the customer experience, this plan offers a clear pathway for continuous refinement. Organizations neglecting process evolution inevitably face competitive disadvantages. Consequently, a rigorous process improvement plan is not merely advantageous—it is indispensable for organizational health and growth.
What Is a Process Improvement Plan?
A process improvement plan outlines the steps an organization will take to analyze, redesign, and optimize a business process. It includes detailed assessments of current workflows, identifies inefficiencies, and proposes specific actions to achieve better performance.
It is commonly used in project management, quality management, Lean Six Sigma, and business process management (BPM) initiatives.
Key Components of a Process Improvement Plan
A well-structured process improvement plan includes several key components that guide the organization from identifying inefficiencies to implementing lasting change. Each component plays a critical role in ensuring that improvements are strategic, measurable, and sustainable.
1. Objectives and Goals
Start by clearly defining what you want to achieve with the process improvement. These goals should align with the organization's broader strategic objectives.
Examples:
- Reduce the customer service response time from 48 hours to 24 hours
- Increase the accuracy of order fulfillment to 99.8%
- Cut costs related to manual invoice processing by 30%
💡Tip: Use SMART goals (Specific, Measurable, Achievable, Relevant, Time-bound) to ensure clarity and accountability.
2. Current State Analysis ("As-Is" Process)
This involves documenting how the process works today. Techniques like process mapping, flowcharts, or swimlane diagrams help visualize each step, identify the actors involved, and clarify handoffs between departments.
What to look for:
- Redundant steps
- Delays or bottlenecks
- Frequent errors or rework
- Unclear responsibilities
👉 Want to dive deeper into how to effectively document and analyze your current workflows? Read our full article on How to Conduct an "as is" business process mapping.
3. Problem Identification and Root Cause Analysis
Once the process is mapped, analyze data and gather input from stakeholders to find the root causes of performance issues. Use tools like the 5 Whys, Pareto Analysis, or Fishbone Diagrams.
Questions to ask:
- Where are delays occurring?
- Why do errors happen?
- What steps create the most cost or waste?
💡Focus on identifying root causes instead of treating symptoms.
4. Proposed Improvements ("To-Be" Process Design)
Redesign the process with efficiency and value in mind. The "to-be" version should eliminate pain points and improve performance based on your defined objectives.
Examples of improvement initiatives:
- Automating repetitive tasks using RPA
- Removing non-value-adding steps
- Reassigning tasks to appropriate roles
- Adding validation steps to reduce errors
👉 Curious to see how other organizations have successfully redesigned their processes? Check out our article featuring real-world Business Process Redesign Success Stories and discover what made their improvements work.
5. Implementation Plan
Detail how the proposed improvements will be put into practice. This section should include action items, responsible parties, deadlines, resources, and risk mitigation strategies.
Include:
- Step-by-step actions
- Timeline (e.g., Gantt chart)
- Responsible teams
- Communication and change management plans
💡Engage stakeholders early to build support and ensure smoother adoption.
6. Key Performance Indicators (KPIs) and Success Metrics
Define measurable criteria that will help assess whether the improvement was successful. Choose KPIs that align with your original goals.
Examples:
- Cycle time
- Error or rework rates
- Satisfaction scores
- Cost per transaction
💡Set specific thresholds so you can track progress and success objectively.
7. Monitoring, Review, and Continuous Feedback
After implementation, continue monitoring the process to ensure improvements are sustained. Establish routines for performance tracking, feedback collection, and periodic reviews.
To sustain improvements:
- Conduct regular audits
- Gather feedback from users
- Reassess and optimize periodically
- Apply continuous improvement models like PDCA (Plan–Do–Check–Act)
Real-World Example: Improving the Employee Onboarding Process
Let’s take a realistic scenario from an HR department in a mid-sized company, where the employee onboarding process was underperforming. New hires were facing delays in receiving work equipment, accessing internal systems, and completing initial training. This led to poor first impressions, low early engagement, and longer ramp-up times.
Background
- Problem Identified: The average onboarding time was 12 business days from the employee's start date to full productivity.
- Symptoms: Delayed IT provisioning, inconsistent onboarding checklists, too much manual paperwork.
- Impact: New hires felt unprepared, managers were frustrated, and HR spent excessive time on repetitive admin tasks.
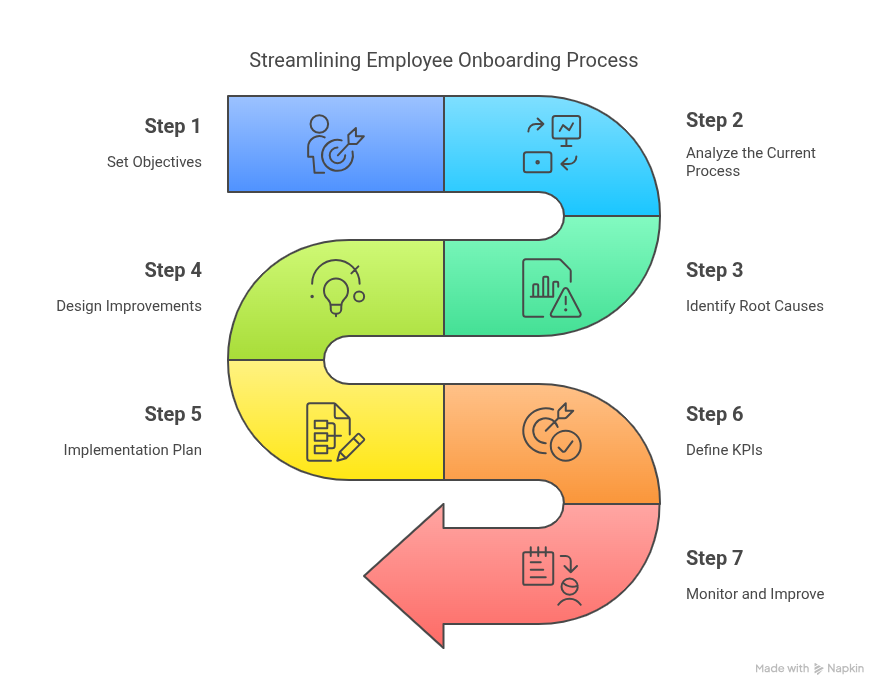
Step 1: Set Objectives
The process improvement plan focused on three main goals:
- Reduce time-to-productivity for new employees.
- Eliminate manual tasks that slow down the onboarding pipeline.
- Create a consistent, high-quality onboarding experience across departments.
Step 2: Analyze the Current Process
The current (as-is) onboarding process involved:
- HR sending offer letters manually via email.
- IT setting up email accounts and laptops only after the employee’s first day.
- No centralized checklist or dashboard for tasks like compliance training or equipment requests.
- Paper forms for tax, benefits, and policies.
A BPMN flowchart revealed that more than 7 handoffs between departments caused delays.
Step 3: Identify Root Causes
Using staff interviews and process audits, the following root issues were discovered:
- HR had no automated triggers for IT to begin provisioning.
- Onboarding steps varied by manager, with no formal checklist.
- Employees had to sign 5+ documents manually.
- Tracking progress relied on Excel sheets and emails.
Step 4: Design Improvements
The redesigned (to-be) process introduced:
- A self-service onboarding portal that triggers tasks automatically when the offer letter is signed.
- An automated workflow to notify IT to start account and equipment setup 7 days before the start date.
- Digital forms with e-signature support for tax and HR documentation.
- Standardized onboarding checklists integrated with the company’s project management tool.
Step 5: Implementation Plan
Action | Owner | Timeline | Tools |
---|---|---|---|
Select onboarding tool (e.g., BambooHR) | HR Manager | 2 weeks | Vendor comparison matrix |
Create automation between HR and IT | IT Lead | 3 weeks | Power Automate, Zapier |
Build and test onboarding checklists | HR & Dept. Heads | 4 weeks | Trello, Asana |
Migrate paper forms to e-signature | HR Operations | 2 weeks | DocuSign |
Launch pilot for 10 new hires | All Teams | 1 month | Full process evaluation |
Step 6: Define KPIs
The team used these success metrics:
- Time to full access: Target under 3 business days
- Employee onboarding satisfaction score: Goal ≥ 4.5/5
- % of forms completed digitally before start: Target 100%
- Onboarding checklist completion rate: Target ≥ 95% in first week
Step 7: Monitor and Improve
- A dashboard was set up to track onboarding KPIs in real time.
- HR collected feedback from new hires 2 weeks after starting.
- Quarterly retrospectives helped refine tasks and eliminate friction points.
Results After 3 Months
- Onboarding time dropped from 12 to 4.8 business days.
- 98% of equipment was delivered before day one.
- 100% of onboarding forms were signed digitally.
- New hire satisfaction improved from 3.8 to 4.6 out of 5.
- Managers reported higher confidence in readiness of new team members.
This example highlights how a structured process improvement plan helped transform a fragmented, manual process into an efficient and employee-friendly experience — ultimately saving time and improving retention.
Final Thoughts
A process improvement plan is more than a document — it's a mindset of continuous optimization. Whether you're working on customer service, procurement, HR, or IT processes, implementing and maintaining a process improvement plan helps your business stay agile, competitive, and efficient.
Finally, the table below outlines a structured study plan to help you master all key topics related to a process improvement plan.