Mastering the PDCA Cycle: Your Roadmap to Effective Continuous Improvement
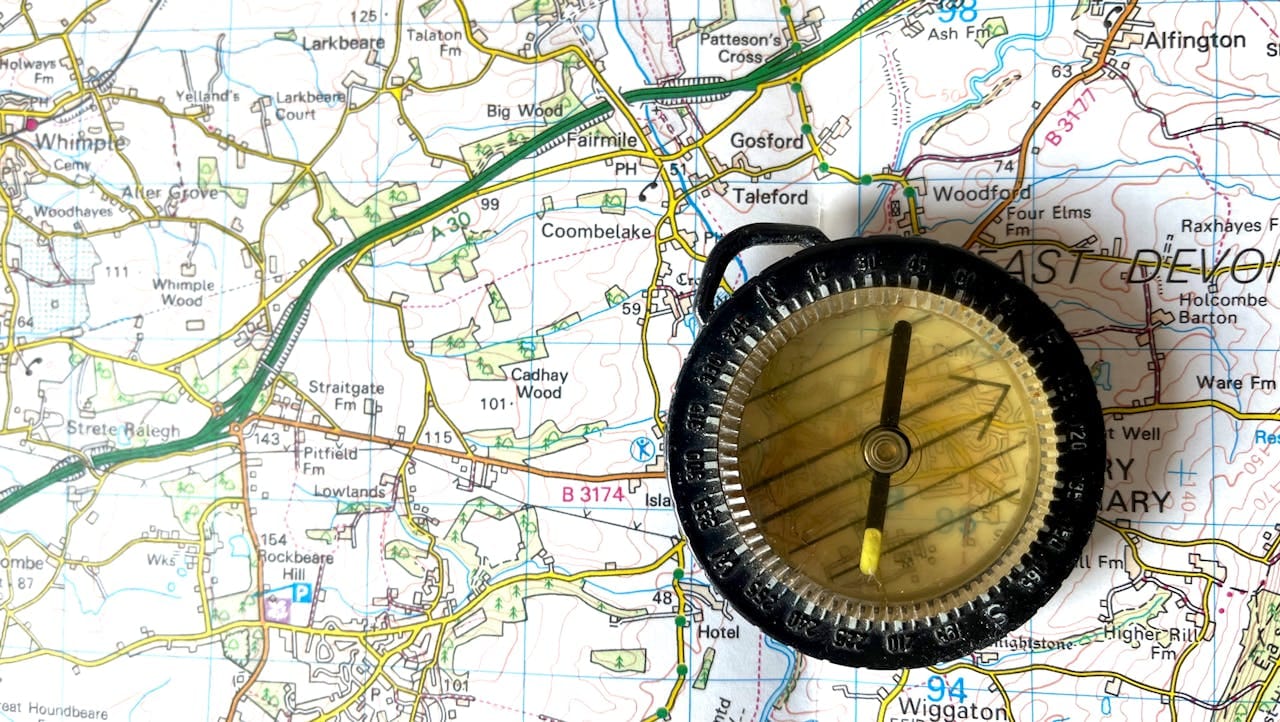
The PDCA Cycle, also known as the Deming Cycle, is a four-step iterative process used for continuous improvement in business process management. Originating from the work of Dr. Edwards Deming in the 1950s, the PDCA Cycle provides a structured framework for problem-solving and process optimization. This methodology is widely adopted due to its simplicity and effectiveness in driving incremental improvements.
History and Origin of PDCA
The PDCA cycle has its roots in the mid-20th century. It was developed as a framework for continuous improvement in business processes and quality management. The cycle's simplicity and universal applicability have made it a cornerstone in various industries, from manufacturing to healthcare.
Origins of PDCA
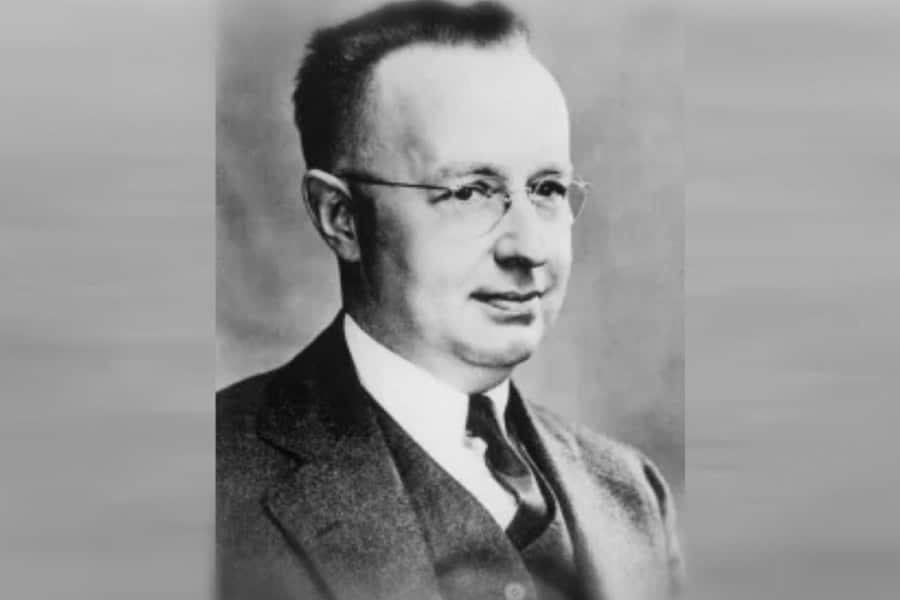
The PDCA cycle was conceptualized by Walter A. Shewhart, a physicist, engineer, and statistician, in the 1920s. Shewhart introduced the concept of a continuous cycle for process improvement, which he initially called the "Shewhart Cycle." His work laid the foundation for modern quality control and process management.
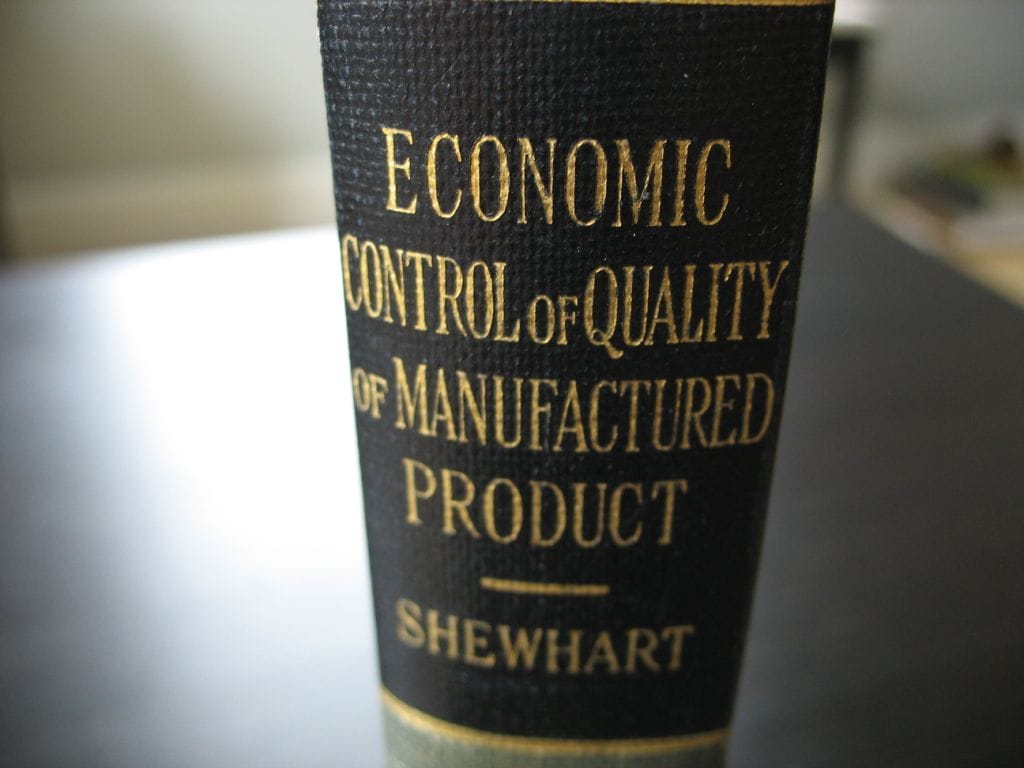
Contribution of Edwards Deming
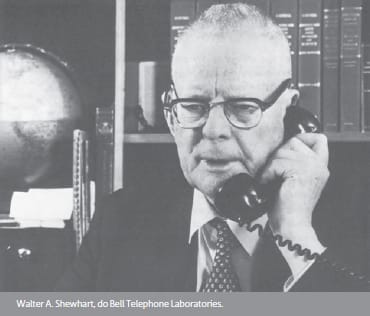
In the 1950s, W. Edwards Deming, an American engineer, statistician, and management consultant, further developed and popularized the cycle. Deming's adaptation of Shewhart's work led to the cycle being widely known as the "Deming Cycle" or "PDCA Cycle." Deming emphasized the importance of the cycle in achieving quality improvement and operational efficiency.
Plan
In the "Plan" phase, objectives and processes are established. This phase involves identifying opportunities for improvement and developing a plan to achieve the desired outcomes.
Do
The "Do" phase involves implementing the plan on a small scale to test its effectiveness. This phase is crucial for identifying any potential issues before full-scale implementation.
Check
During the "Check" phase, the outcomes of the "Do" phase are evaluated. This involves measuring performance and comparing it against the expected results to identify any discrepancies.
Act
In the "Act" phase, successful strategies are standardized and implemented on a larger scale. If the plan did not work as expected, this phase involves identifying the issues and making necessary adjustments before repeating the cycle.
Understanding the Plan Phase
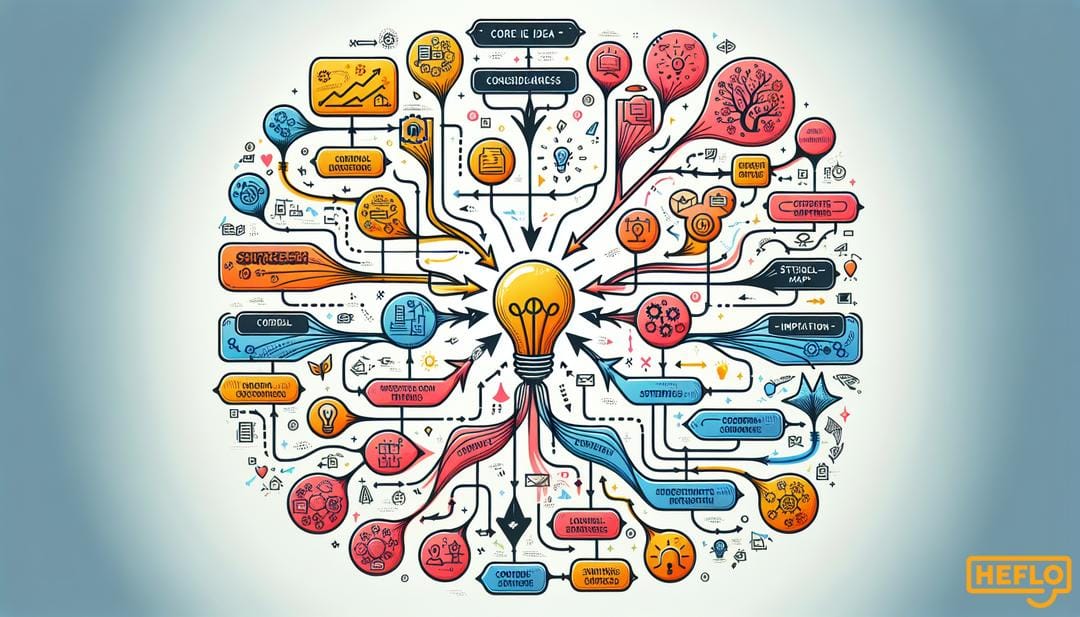
The Plan Phase of the PDCA Lifecycle is designed to ensure that both the business process context and internal process design align with the organization’s strategic objectives. This phase is foundational as it sets the stage for all subsequent actions and decisions within the cycle.
The beginning is the most important part of the work. - Plato
Defining Objectives and Goals
In the Plan Phase, the first step is to clearly define the objectives and goals that the process aims to achieve. These should be aligned with the broader strategic objectives of the organization. This alignment ensures that the process contributes to the overall mission and vision of the company.
Analyzing Current Processes
Before any new plans can be made, it is essential to analyze the current processes. This involves understanding the existing workflows, identifying bottlenecks, and recognizing areas for improvement. Tools like SWOT analysis (Strengths, Weaknesses, Opportunities, Threats) can be useful in this stage.
Designing Future-State Processes
Once the current processes are understood, the next step is to design the future-state processes. This involves creating detailed process maps that outline the desired workflow, roles, responsibilities, and performance metrics. The design should be robust enough to meet the defined objectives and flexible enough to adapt to changes.
Setting Performance Metrics
Performance metrics are critical in the Plan Phase as they provide the benchmarks against which process performance will be measured. These metrics should cover various aspects such as timeliness, product quality, service quality, cost, and customer satisfaction. Setting clear, measurable targets helps in tracking progress and identifying areas for improvement.
Risk Assessment and Mitigation
Identifying potential risks and developing mitigation strategies is another crucial aspect of the Plan Phase. This involves conducting a risk assessment to identify possible challenges and creating contingency plans to address them. Effective risk management ensures that the process can withstand uncertainties and continue to function smoothly.
Resource Allocation
Proper resource allocation is essential for the successful implementation of the plan. This includes assigning the right personnel, budgeting for necessary tools and technologies, and ensuring that all stakeholders are on board. Adequate resource planning helps in avoiding delays and ensures that the process runs efficiently.
Key Elements of the Do Phase
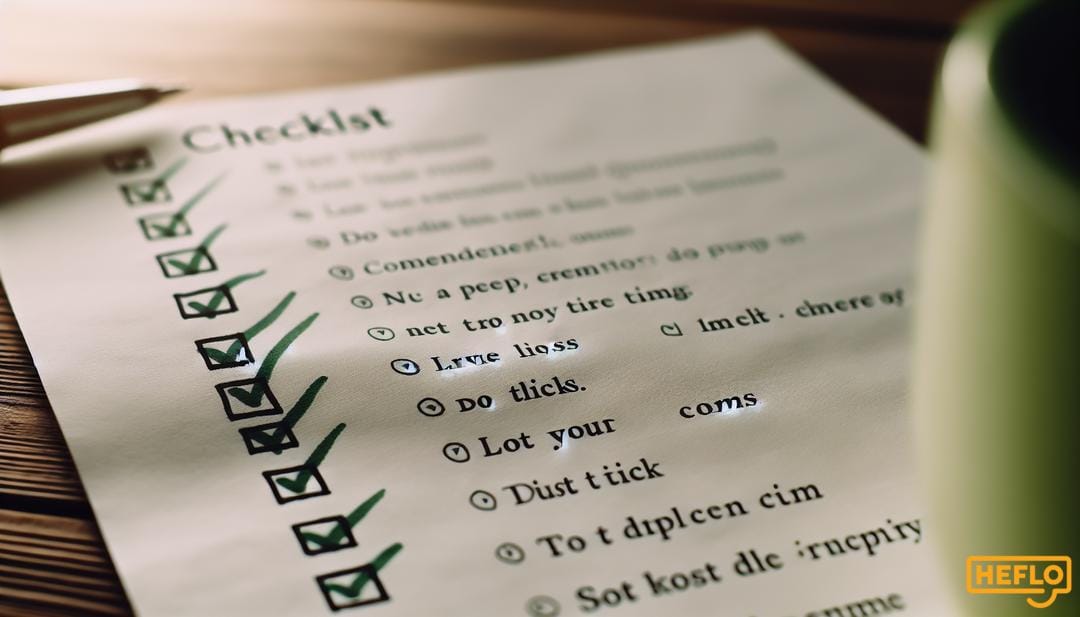
The "Do" phase of the PDCA Lifecycle is where the rubber meets the road. This phase involves the actual implementation of the plans and strategies developed during the "Plan" phase. It is a critical step that transitions theoretical plans into actionable tasks, ensuring that the process is executed as designed.
Process Deployment
During the "Do" phase, the process is deployed according to the specifications laid out in the "Plan" phase. This involves:
- Triggering the process through initiating events
- Receiving process inputs
- Executing activities
- Producing sub-deliverables
- Generating and delivering process outputs
Execution and Monitoring
Once the process is deployed, it is essential to monitor its execution to ensure it aligns with the planned objectives. This includes:
- Tracking the progress of activities
- Ensuring that deliverables meet quality standards
- Identifying any deviations from the plan
- Implementing corrective actions as needed
Role of Technology
Technology plays a significant role in the "Do" phase. Information systems and workflow automation tools can help streamline the execution of processes, making them more efficient and less prone to errors. These tools can also provide real-time data that is crucial for monitoring and making timely adjustments.
Feedback Loop
The "Do" phase is not just about execution; it also involves gathering data and feedback that will be used in the subsequent "Check" phase. This feedback loop is essential for continuous improvement, as it helps identify areas for enhancement and ensures that the process remains aligned with organizational goals.
Analyzing the Check Phase
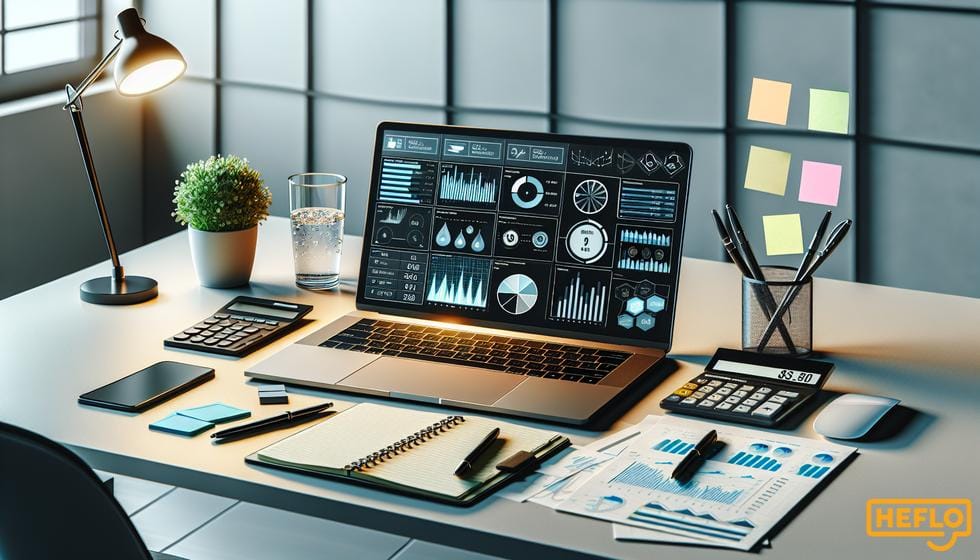
The "Check" phase of the PDCA cycle is where the rubber meets the road in terms of evaluating the effectiveness of implemented processes. This phase involves a thorough examination of process performance data to determine whether the outcomes align with the set performance expectations. By systematically measuring and analyzing various performance metrics, organizations can identify areas of improvement and make informed decisions for future actions.
Key Performance Metrics
In the "Check" phase, several traditional categories of performance measures are utilized to gauge the effectiveness of processes:
- Timeliness: Metrics such as throughput, cycle time, and delivery dates help assess how efficiently processes are being executed.
- Product Quality: Measures like defect rates, rework volume, and product reliability provide insights into the quality of the output.
- Service Quality: Responsiveness, trustworthiness, and service reliability are critical for evaluating the quality of service provided.
- Cost: Labor, material, overhead, and rework costs are analyzed to understand the financial efficiency of processes.
- Customer Satisfaction: Customer feedback and satisfaction levels indicate whether the product or service meets customer expectations.
Data Collection and Analysis
Data collection in the "Check" phase is comprehensive, involving real-time, near-term, and long-term data from various sources. This data feeds into the decision-making process in the "Do" phase and helps in identifying performance gaps and areas for improvement.
Real-Time and Near-Real-Time Monitoring
Real-time and near-real-time performance monitoring allows organizations to quickly identify and respond to issues as they arise. This proactive approach ensures that any deviations from expected performance are promptly addressed, minimizing potential negative impacts.
Performance Reporting
Effective performance reporting ensures that relevant data is available at the right time and in the right format for decision-makers at all levels of the organization. This includes detailed reports for operational staff and high-level summaries for executives.
Implementing the Act Phase
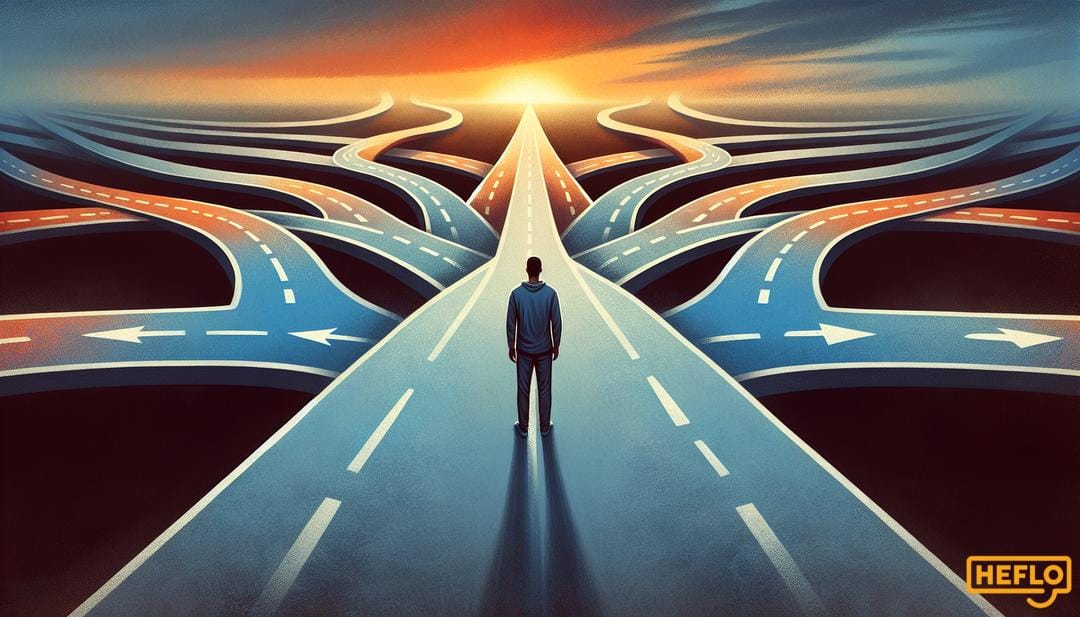
This phase is all about making informed decisions and taking appropriate actions based on the data collected and analyzed during the "Check" phase. The goal is to ensure that processes remain effective and continue to improve over time, even in the face of changing environments.
Quality is not an act, it is a habit. - Aristotle
Data Collection and Aggregation
The first step in the Act phase involves gathering all the data and observations collected during the Check phase. This data can come from various sources, including performance metrics, customer feedback, and internal audits. The key is to ensure that the data is comprehensive and accurately reflects the current state of the process.
Analyzing Data for Criticality and Impact
Once the data is collected, the next step is to analyze it to determine its criticality and impact. This involves identifying which issues are most urgent and which have the most significant impact on the process. For example, if a high percentage of workspace setups are not completed on time, this issue would be flagged as critical and require immediate attention.
Developing Recommendations
Based on the analysis, recommendations are developed to address each identified issue. These recommendations should be specific, actionable, and designed to improve the process. For instance, if Human Resource Specialists are dissatisfied with the current technologies for pre-employment screening, a recommendation might be to invest in new software solutions.
Ranking and Prioritization
After developing recommendations, the next step is to rank and prioritize them. This ensures that the most critical and impactful changes are addressed first. Prioritization can be based on various factors, including the potential for improvement, resource availability, and alignment with organizational goals.
Implementing Changes
Once the recommendations are prioritized, the next step is to implement the changes. This may involve updating process documentation, retraining staff, or investing in new technologies. The key is to ensure that the changes are effectively communicated and that all stakeholders are on board.
Monitoring and Feedback
After implementing the changes, it's crucial to monitor their impact and gather feedback. This helps to ensure that the changes are having the desired effect and allows for further adjustments if necessary. Continuous monitoring and feedback are essential for ongoing process improvement.
Benefits of Using the PDCA Cycle
Implementing the PDCA (Plan-Do-Check-Act) Cycle offers numerous advantages for organizations aiming to enhance their processes and achieve continuous improvement. This iterative method, rooted in the principles of quality management, provides a structured approach to problem-solving and process optimization.
Enhanced Process Performance
The PDCA Cycle facilitates the continuous monitoring and evaluation of process performance. By systematically measuring key performance indicators (KPIs) such as timeliness, product quality, service quality, cost, and customer satisfaction, organizations can identify areas for improvement and make data-driven decisions.
Timeliness
Metrics like throughput, cycle time, and delivery dates help in assessing whether processes are meeting time-related goals. This ensures that operations are efficient and deadlines are consistently met.
Product and Service Quality
By tracking defects, rework volumes, and reliability, organizations can maintain high standards of product quality. Similarly, service quality metrics such as responsiveness and trustworthiness ensure that customer expectations are met or exceeded.
Cost Management
Monitoring labor, material, and overhead costs, as well as the cost of rework, helps in identifying cost-saving opportunities and improving overall financial performance.
Explore more insights in the video below on the role of cost reduction engineer.
Customer Satisfaction
Regularly measuring customer perceptions and satisfaction levels ensures that the products or services provided align with customer expectations, fostering loyalty and repeat business.
Proactive Response to Change
The PDCA Cycle's "Act" phase enables organizations to respond proactively to changes in the environment. By analyzing data collected during the "Check" phase, businesses can adapt their processes to maintain integrity and meet new performance goals.
Structured Problem-Solving
The PDCA Cycle provides a clear framework for identifying, analyzing, and addressing issues. This structured approach ensures that problems are thoroughly investigated and solutions are effectively implemented.
Continuous Improvement
One of the core benefits of the PDCA Cycle is its emphasis on continuous improvement. By iterating through the cycle, organizations can make incremental changes that lead to significant long-term improvements in process efficiency and effectiveness.
Common Pitfalls and How to Avoid Them
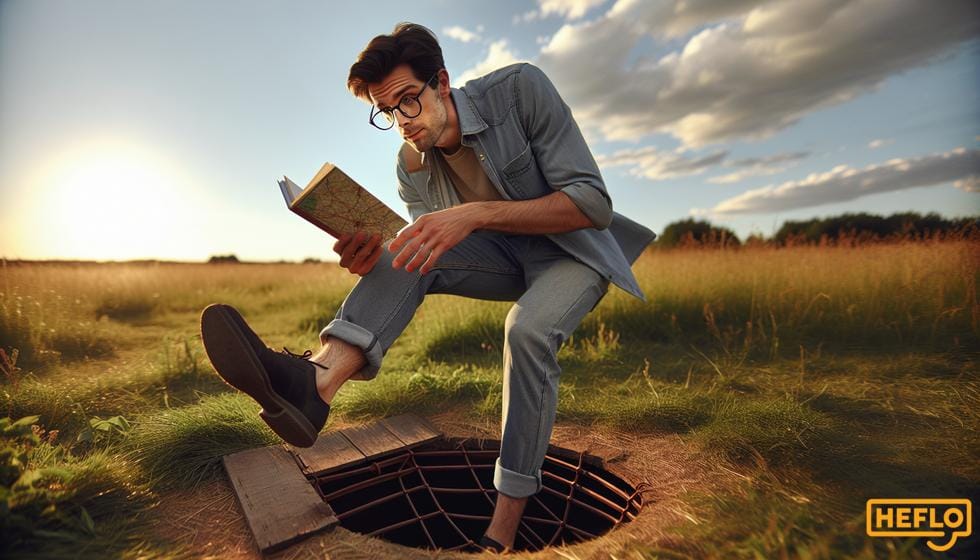
When implementing the PDCA (Plan-Do-Check-Act) cycle, organizations often encounter several common pitfalls that can hinder the effectiveness of their continuous improvement efforts. Understanding these pitfalls and knowing how to avoid them can significantly enhance the success of the PDCA cycle.
Inadequate Planning
One of the most frequent pitfalls is inadequate planning. Without a clear and detailed plan, the subsequent phases of the PDCA cycle can become disorganized and ineffective.
- Solution: Invest time in thorough planning. Define clear objectives, identify necessary resources, and establish measurable targets. Ensure that all stakeholders are aligned with the plan.
Poor Data Collection and Analysis
Another common issue is the collection of insufficient or inaccurate data during the "Check" phase. This can lead to misguided actions and suboptimal improvements.
- Solution: Implement robust data collection methods and ensure data accuracy. Utilize advanced analytics tools to gain deeper insights into process performance.
Resistance to Change
Resistance from employees and other stakeholders can significantly impede the implementation of improvements identified in the PDCA cycle.
- Solution: Foster a culture of continuous improvement and open communication. Engage stakeholders early in the process and provide training to ease the transition.
Learn how to handle resistance to change by watching our change management video.
Lack of Follow-Through
Failing to follow through on the actions identified in the "Act" phase can result in missed opportunities for improvement and a lack of progress.
- Solution: Establish accountability mechanisms and regularly review progress. Ensure that actions are tracked and completed as planned.
Overlooking Long-Term Sustainability
Focusing solely on short-term gains without considering long-term sustainability can lead to recurring issues and inefficiencies.
- Solution: Balance short-term and long-term goals. Develop strategies that ensure sustainable improvements and continuous monitoring.
Tools and Techniques for Each Phase
Implementing continuous improvement within an organization involves a systematic approach to refining processes and enhancing performance. This journey can be effectively navigated using various tools and techniques tailored to each phase of the PDCA (Plan-Do-Check-Act) cycle.
Quality is never an accident; it is always the result of intelligent effort. - John Ruskin
Plan Phase
In the Plan phase, the focus is on identifying opportunities for improvement and devising strategies to address them. Key tools and techniques include:
- SWOT Analysis: Evaluates strengths, weaknesses, opportunities, and threats to understand the current state and potential areas for improvement.
- Root Cause Analysis: Identifies the underlying causes of issues to ensure that solutions address the core problems.
- Benchmarking: Compares processes and performance metrics to industry standards or best practices to set realistic improvement goals.
Do Phase
The Do phase involves implementing the planned changes. Effective tools and techniques for this phase include:
- Project Management: Utilizes methodologies like Agile or Waterfall to manage the execution of improvement initiatives.
- Standard Operating Procedures (SOPs): Provides detailed instructions to ensure consistent execution of new processes.
- Training Programs: Equips employees with the necessary skills and knowledge to adapt to new processes.
Check Phase
In the Check phase, the focus is on measuring and analyzing the performance of implemented changes. Key tools and techniques include:
- Performance Metrics: Measures timeliness, product quality, service quality, cost, and customer satisfaction to evaluate process performance.
- Data Analytics: Analyzes collected data to identify trends, patterns, and areas for further improvement.
- Dashboards: Provides real-time visualization of key performance indicators (KPIs) to facilitate quick decision-making.
Act Phase
The Act phase involves making decisions based on the data collected in the Check phase and implementing necessary adjustments. Effective tools and techniques for this phase include:
- Continuous Improvement Programs: Establishes ongoing initiatives to refine processes and address emerging issues.
- Feedback Loops: Ensures that insights from the Check phase are fed back into the planning process for continuous refinement.
- Change Management: Manages the human aspect of change to ensure smooth transitions and sustained improvements.
Integrating PDCA with Other Improvement Methods
Integrating the PDCA (Plan-Do-Check-Act) cycle with other improvement methods can significantly enhance an organization's ability to achieve continuous improvement. By combining PDCA with methodologies such as Lean, Six Sigma, and Business Process Management (BPM), organizations can leverage the strengths of each approach to create a more robust and effective improvement strategy.
Combining PDCA with Lean
Lean methodology focuses on eliminating waste and improving process efficiency. When integrated with PDCA, Lean principles can be systematically applied to identify inefficiencies (Plan), implement changes (Do), monitor results (Check), and standardize successful practices (Act). This integration ensures that Lean improvements are continuously evaluated and refined.
Integrating PDCA with Six Sigma
Six Sigma aims to reduce process variation and improve quality through a data-driven approach. By incorporating PDCA, Six Sigma projects can benefit from a structured cycle of planning, executing, checking, and acting on improvements. This combination allows for rigorous analysis (Plan), controlled implementation (Do), thorough evaluation (Check), and informed adjustments (Act).
Enhancing BPM with PDCA
Business Process Management (BPM) involves the holistic management of business processes to achieve organizational goals. Integrating PDCA into BPM initiatives ensures that processes are not only designed and implemented effectively but are also continuously monitored and improved. The PDCA cycle provides a framework for ongoing process optimization within the BPM discipline.
In conclusion, mastering the PDCA-cycle is not just a strategy but a transformative journey towards achieving effective continuous improvement. By diligently applying the Plan-Do-Check-Act methodology, organizations can foster a culture of perpetual growth, innovation, and excellence. The PDCA-cycle empowers teams to systematically address challenges, optimize processes, and enhance overall performance. As you embark on this roadmap, remember that the essence of the PDCA-cycle lies in its iterative nature—each cycle brings you closer to your goals, driving sustainable success and long-term value. Embrace the PDCA-cycle, and let it be the cornerstone of your continuous improvement endeavors.