The Power of Kaizen: How Continuous Improvement Drives Success
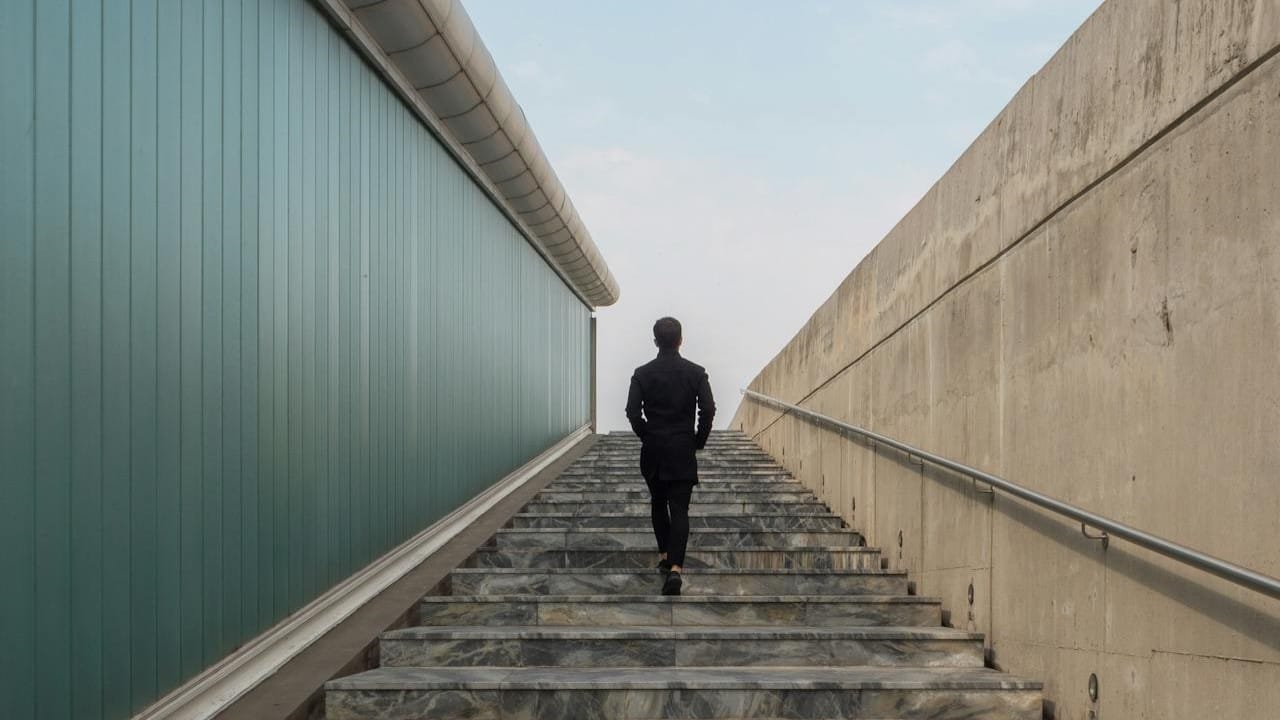
Kaizen, a Japanese term meaning "change for better," is a philosophy that focuses on continuous improvement in all aspects of life, particularly in business processes. Originating in Japan after World War II, Kaizen has since become a cornerstone of modern management practices worldwide. It emphasizes small, incremental changes rather than large-scale transformations, fostering a culture where employees at all levels are encouraged to contribute ideas for improvement.
Great things are not done by impulse, but by a series of small things brought together. - Vincent Van Gogh
At its core, Kaizen is about making ongoing, positive changes that enhance efficiency, productivity, and quality. This approach is not limited to manufacturing but is applicable across various industries, including healthcare, finance, and technology. By involving everyone from top management to frontline workers, Kaizen creates a sense of ownership and accountability, leading to more sustainable improvements.
One of the key principles of Kaizen is the belief that every process can be improved. This mindset encourages organizations to constantly evaluate their operations, identify areas of waste, and implement solutions to eliminate inefficiencies. Techniques such as the Plan-Do-Check-Act (PDCA) cycle and the 5S methodology (Sort, Set in order, Shine, Standardize, Sustain) are commonly used to facilitate this continuous improvement process.
Another important aspect of Kaizen is its focus on teamwork and collaboration. By fostering an environment where employees feel valued and empowered to share their ideas, organizations can tap into a wealth of knowledge and creativity. This collaborative approach not only leads to better solutions but also enhances employee morale and engagement.
Principles of Continuous Improvement
Continuous improvement, often associated with the Japanese term "Kaizen," is a systematic approach to enhancing processes, products, and services. It involves making small, incremental changes that collectively lead to significant improvements over time. This methodology is rooted in several core principles that guide organizations in their pursuit of excellence.
Focus on Customer Value
One of the fundamental principles is to prioritize customer value. Understanding and meeting customer needs and expectations is paramount. By continuously seeking feedback and making adjustments based on this input, organizations can ensure they are delivering maximum value.
Employee Involvement
Engaging employees at all levels is essential for successful continuous improvement. Employees are often the best source of ideas for enhancing processes since they are directly involved in the day-to-day operations. Encouraging a culture where everyone feels empowered to suggest improvements fosters innovation and ownership.
Standardization
Standardizing processes is another key principle. By establishing clear, consistent procedures, organizations can ensure that improvements are sustainable and repeatable. Standardization helps in maintaining quality and efficiency, making it easier to identify areas for further enhancement.
Data-Driven Decision Making
Making decisions based on data rather than intuition is crucial. Collecting and analyzing relevant data allows organizations to identify trends, measure performance, and make informed decisions. This approach minimizes risks and increases the likelihood of successful outcomes.
Incremental Changes
Rather than seeking radical changes, continuous improvement focuses on making small, incremental adjustments. These minor tweaks can accumulate over time, leading to substantial improvements. This principle helps in managing change more effectively and reduces resistance from employees.
Continuous Learning
Finally, fostering a culture of continuous learning is vital. Organizations should encourage ongoing education and training to keep employees updated with the latest knowledge and skills. This commitment to learning ensures that the workforce remains adaptable and capable of driving continuous improvement.
Unlock the secrets of Continuous Improvement by watching this exclusive, handpicked YouTube video!
Implementing Kaizen in the Workplace
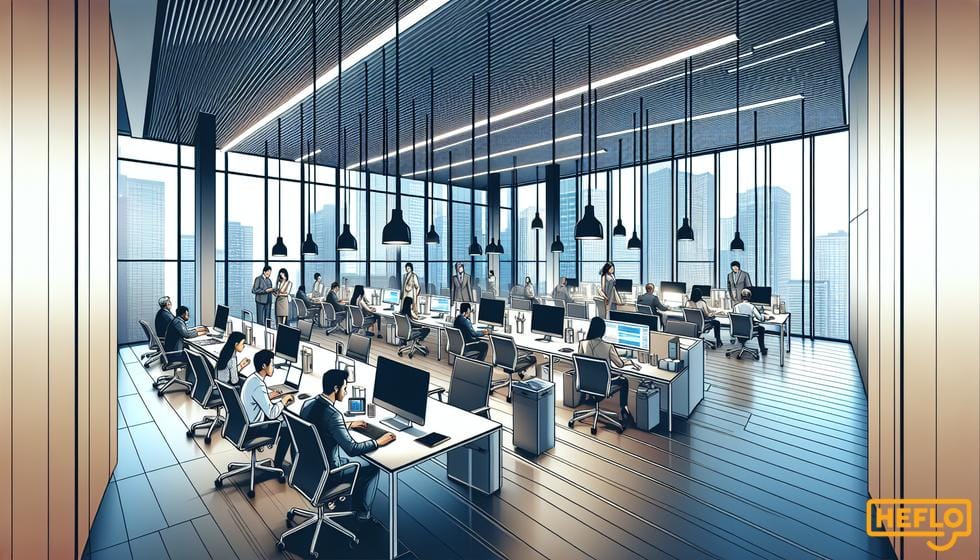
Kaizen is a philosophy that focuses on continuous improvement in all aspects of life, including the workplace. By implementing Kaizen, companies can foster a culture of ongoing enhancement, where every employee is encouraged to contribute ideas for improving processes, products, and services.
One of the key principles of Kaizen is involving everyone in the organization, from top management to frontline workers. This inclusive approach ensures that improvements are not just top-down directives but are also driven by those who are directly involved in the processes. Employees are empowered to identify inefficiencies and suggest practical solutions, leading to a more engaged and motivated workforce.
Another important aspect of Kaizen is its focus on small, incremental changes rather than large, disruptive overhauls. This makes it easier to implement and sustain improvements over time. Small changes can add up to significant enhancements in productivity, quality, and overall efficiency. Regularly reviewing and refining processes helps in maintaining a competitive edge and adapting to changing market conditions.
Incorporating Kaizen into the workplace also promotes a culture of learning and development. Employees are encouraged to acquire new skills and knowledge, which can lead to innovative solutions and better problem-solving capabilities. This not only enhances individual performance but also contributes to the overall growth and success of the organization.
For companies looking to document and automate their business processes, integrating Kaizen principles can be highly beneficial. Tools like HEFLO can assist in mapping out processes, identifying areas for improvement, and tracking the impact of implemented changes. This structured approach ensures that continuous improvement efforts are well-organized and measurable.
Watch our latest video on business process automation and discover how to transform your organization for maximum efficiency. Don't miss out – your path to better business starts here!
Benefits of Kaizen
One of the primary benefits of Kaizen is its ability to foster a culture of continuous improvement within an organization. By encouraging employees at all levels to contribute ideas for process enhancements, companies can tap into a wealth of knowledge and creativity. This inclusive approach not only improves processes but also boosts employee morale and engagement.
Another significant advantage of Kaizen is its impact on efficiency. By continuously identifying and eliminating waste, businesses can streamline their operations, reduce costs, and improve productivity. This focus on efficiency helps companies remain competitive in an ever-evolving market.
Kaizen also promotes better quality control. Through regular, incremental improvements, businesses can identify and address quality issues before they become major problems. This proactive approach leads to higher-quality products and services, which in turn enhances customer satisfaction and loyalty.
Moreover, Kaizen encourages a proactive mindset. Instead of waiting for problems to arise, employees are trained to anticipate potential issues and address them before they escalate. This forward-thinking approach not only prevents disruptions but also fosters a more resilient and adaptable organization.
Case Studies and Real-World Applications
Kaizen, the Japanese philosophy of continuous improvement, has been successfully implemented across various industries, demonstrating its versatility and effectiveness. By focusing on small, incremental changes, organizations can achieve significant improvements in efficiency, productivity, and overall performance.
One notable example is Toyota, where Kaizen originated. The company has integrated Kaizen into its production system, leading to remarkable advancements in manufacturing processes. By encouraging employees at all levels to suggest improvements, Toyota has been able to reduce waste, enhance quality, and increase production speed. This approach has played a crucial role in establishing Toyota as a global leader in the automotive industry.
In the healthcare sector, Virginia Mason Medical Center in Seattle adopted Kaizen principles to improve patient care and operational efficiency. By implementing continuous improvement strategies, the hospital reduced patient waiting times, minimized errors, and enhanced overall patient satisfaction. The success of Kaizen at Virginia Mason has inspired other healthcare institutions to adopt similar practices.
Another compelling case is that of the British retailer Tesco. Facing intense competition and market challenges, Tesco turned to Kaizen to streamline its operations and improve customer service. By fostering a culture of continuous improvement, Tesco was able to optimize its supply chain, reduce costs, and enhance the shopping experience for its customers. This transformation helped Tesco regain its competitive edge in the retail market.
In the world of software development, companies have embraced Kaizen to enhance their development processes. By continuously refining their workflows, these organizations have been able to deliver higher-quality software products more efficiently. This iterative approach has proven to be particularly effective in the fast-paced tech industry, where adaptability and rapid innovation are key to success.
These case studies illustrate the power of Kaizen in driving success across diverse sectors. By fostering a culture of continuous improvement, organizations can achieve remarkable results and maintain a competitive advantage in their respective industries.
In conclusion, the power of Kaizen lies in its ability to foster a culture of continuous improvement, driving both individual and organizational success. By embracing the principles of Kaizen, businesses can achieve incremental advancements that collectively lead to significant progress over time. This approach not only enhances efficiency and productivity but also empowers employees to take ownership of their roles and contribute to the overall growth of the organization. Ultimately, the practice of continuous improvement through Kaizen is a testament to the idea that small, consistent efforts can yield remarkable results, paving the way for sustained success and innovation.