Maximizing Efficiency: A Comprehensive Look at the Cost Reduction Engineer Role and Responsibilities
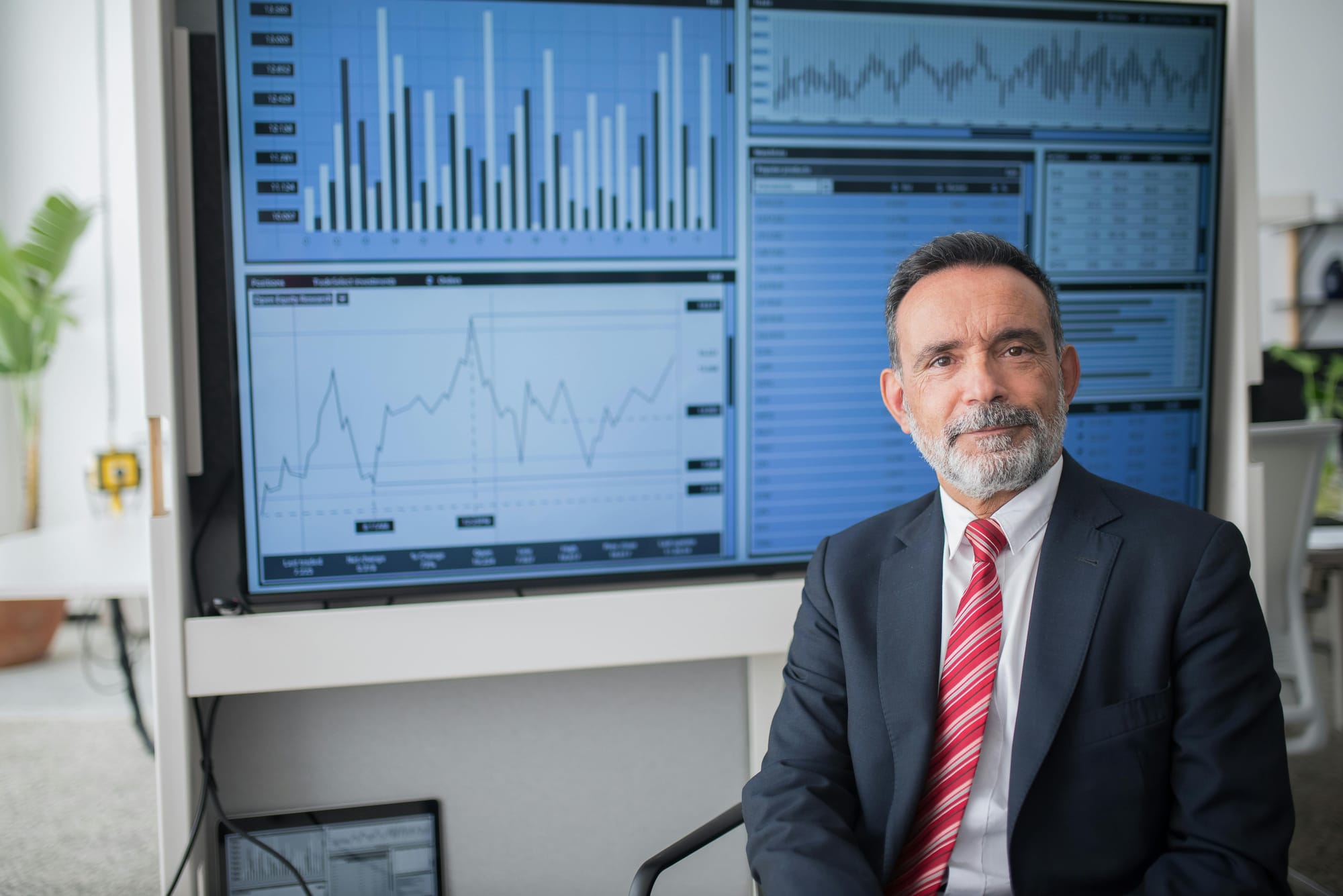
The role of a Cost Reduction Engineer is pivotal in driving operational efficiency and financial savings within an organization. This specialized position focuses on identifying, analyzing, and implementing strategies to reduce costs without compromising on quality or performance. The scope of this role extends across various departments, requiring a deep understanding of engineering principles, financial acumen, and strategic planning.
Cost Reduction Engineers are tasked with conducting thorough assessments of current processes, materials, and technologies to pinpoint areas where cost savings can be achieved. They collaborate closely with cross-functional teams, including procurement, production, and quality assurance, to develop and execute cost-saving initiatives. Their expertise in lean manufacturing, value engineering, and process optimization is crucial in streamlining operations and eliminating waste.
In addition to technical skills, Cost Reduction Engineers must possess strong analytical abilities to evaluate cost-benefit scenarios and forecast the financial impact of proposed changes. They are responsible for creating detailed reports and presentations to communicate their findings and recommendations to senior management. Effective communication and project management skills are essential, as these engineers often lead cost reduction projects from inception to completion.
The scope of the role also includes staying abreast of industry trends and advancements in technology that could offer new opportunities for cost savings. They must be proactive in researching and implementing innovative solutions that enhance efficiency and reduce expenses. This continuous improvement mindset is vital for maintaining a competitive edge in the market.
Overall, the Cost Reduction Engineer plays a critical role in ensuring that an organization operates efficiently and sustainably. By leveraging their technical expertise and strategic insight, they contribute significantly to the company's bottom line and long-term success.
Unlock the secrets of a cost reduction project with this exclusive YouTube video! Don't miss out on this must-watch content.
Key Responsibilities
The role of a Cost Reduction Engineer ensures that an organization operates at maximum efficiency while minimizing expenses. This multifaceted position encompasses a variety of responsibilities that are crucial for achieving cost-effective operations without compromising on quality or performance.
1. Cost Analysis and Assessment
One of the primary responsibilities of a Cost Reduction Engineer is to conduct thorough cost analyses. This involves evaluating current expenditures, identifying areas where costs can be reduced, and assessing the financial impact of potential changes. The engineer must be adept at using various analytical tools and methodologies to gather and interpret data effectively.
2. Process Optimization
Process optimization is at the heart of cost reduction. The engineer is responsible for scrutinizing existing processes to identify inefficiencies and bottlenecks. By implementing streamlined procedures and adopting best practices, the engineer aims to enhance productivity and reduce waste. This may involve reengineering workflows, adopting new technologies, or refining operational strategies.
3. Supplier and Vendor Management
Effective supplier and vendor management is another critical responsibility. The Cost Reduction Engineer must negotiate favorable terms, seek out cost-effective suppliers, and establish long-term partnerships that benefit the organization. This includes evaluating supplier performance, ensuring quality standards are met, and exploring opportunities for bulk purchasing or alternative sourcing.
4. Budgeting and Forecasting
Accurate budgeting and forecasting are essential for maintaining financial health. The engineer plays a key role in developing budgets that reflect cost-saving initiatives and forecasting future expenses. This requires a deep understanding of the organization's financial landscape and the ability to predict the financial outcomes of various cost reduction strategies.
5. Cross-Functional Collaboration
Collaboration with other departments is vital for the successful implementation of cost reduction measures. The Cost Reduction Engineer must work closely with teams such as procurement, production, and finance to ensure that cost-saving initiatives are aligned with overall business objectives. Effective communication and teamwork are essential for driving organization-wide efficiency improvements.
Skills and Qualifications
The role of a Cost Reduction Engineer requires a combination of technical skills, analytical abilities, and industry-specific knowledge. Below are the key skills and qualifications required for a Cost Reduction Engineer:
Technical Skills
- Engineering Expertise: A strong foundation in engineering principles, typically with a degree in industrial, mechanical, or manufacturing engineering.
- Data Analysis: Proficiency in data analysis tools and software to interpret complex data sets and identify cost-saving opportunities.
- Process Improvement: Knowledge of methodologies such as Lean, Six Sigma, and Kaizen to streamline processes and eliminate waste.
- Software Proficiency: Familiarity with ERP systems, CAD software, and other relevant engineering tools.
For companies looking to scale repetitive and voluminous business processes, leveraging tools like HEFLO can significantly enhance the efficiency and effectiveness of a Cost Reduction Engineer's efforts.
Watch our latest video on business process documentation and discover how to transform your organization for maximum efficiency. Don't miss out – your path to better business starts here!.
Analytical Abilities
- Problem-Solving: Strong problem-solving skills to identify inefficiencies and develop effective solutions.
- Critical Thinking: Ability to critically evaluate processes and make data-driven decisions.
- Attention to Detail: Meticulous attention to detail to ensure accuracy in cost analysis and reporting.
Industry-Specific Knowledge
- Industry Standards: Understanding of industry standards and regulations to ensure compliance and optimize processes.
- Market Trends: Awareness of market trends and technological advancements to stay ahead in cost reduction strategies.
Soft Skills
- Communication: Excellent communication skills to effectively collaborate with cross-functional teams and present findings to stakeholders.
- Project Management: Strong project management skills to oversee cost reduction initiatives from conception to implementation.
- Team Collaboration: Ability to work collaboratively in a team environment to achieve common goals.
Tools and Techniques
Here, a variety of tools and techniques are employed, each tailored to address specific aspects of the business process.
One of the primary techniques involves the analysis of current workflows to identify areas of unnecessary motion, waiting time, and transportation steps. By redesigning these workflows, the engineer can uncover and eliminate material-related bottlenecks and disconnections, thereby streamlining operations.
Another critical tool is the pragmatic review of best practices across all process variations currently in use. This involves ensuring that each action within a process adds value and that data or product inputs are managed close to their source. By standardizing best practices and designing process controls, variations, exceptions, and errors can be significantly reduced or eliminated.
Minimizing handoffs and reducing role specializations or organizational silos are also essential techniques. These strategies help in maintaining a smooth flow of operations and reducing delays caused by unnecessary dependencies.
Variation management is another crucial aspect, especially in mass production industries. Excessive variation can slow down processes and require more resources to scale. By identifying and reducing unnecessary variations, the overall cycle-time of the process can be improved. Automation can play a significant role in this, helping to eliminate variations and standardize processes.
Cost analysis is a fundamental tool used by Cost Reduction Engineers. Understanding the total cost of executing a process, including its frequency and circumstances, helps prioritize which processes need early attention. Discussions around cost often focus on whether the cost is in line with industry best practices and how it can be reduced through automation or technology improvements. The impact on realized value and operating margins is also considered to make processes more cost-efficient.
Incorporating these tools and techniques allows Cost Reduction Engineers to drive significant improvements in efficiency and cost reduction. For companies looking to scale repetitive and voluminous business processes, leveraging a cloud business process management system like HEFLO can be highly beneficial.
Impact and Benefits
By focusing on minimizing extra motion, waiting time, and transportation steps, these engineers can significantly add value through the redesign of work processes. This type of analysis often uncovers unnecessary motions and material-related bottlenecks, leading to more streamlined operations.
One of the primary benefits of this role is the ability to minimize handoffs and ensure that each action within a process adds value. By managing data or product inputs close to the source, Cost Reduction Engineers can deliver significant improvements with very low risk. This approach not only enhances process efficiency but also ensures that all participants execute the same best practices accurately.
The team led by a Cost Reduction Engineer can drive process efficiency and effectiveness through a pragmatic review of current best practices from all process variations in use. By designing process controls and guidance, they can ensure the consistent execution of these best practices, thereby reducing or eliminating variations, exceptions, and errors.
Moreover, the impact of a Cost Reduction Engineer extends to the overall organizational performance. By implementing these optimized processes, companies can achieve higher productivity levels, reduced operational costs, and improved product quality. This role is essential in fostering a culture of continuous improvement and operational excellence.
To conclude this topic, we recommend watching the video below on Lean Manufacturing, a production methodology that focuses on improving efficiency and reducing waste.