Streamline Your Production Process: How to Eliminate Bottlenecks and Boost Efficiency
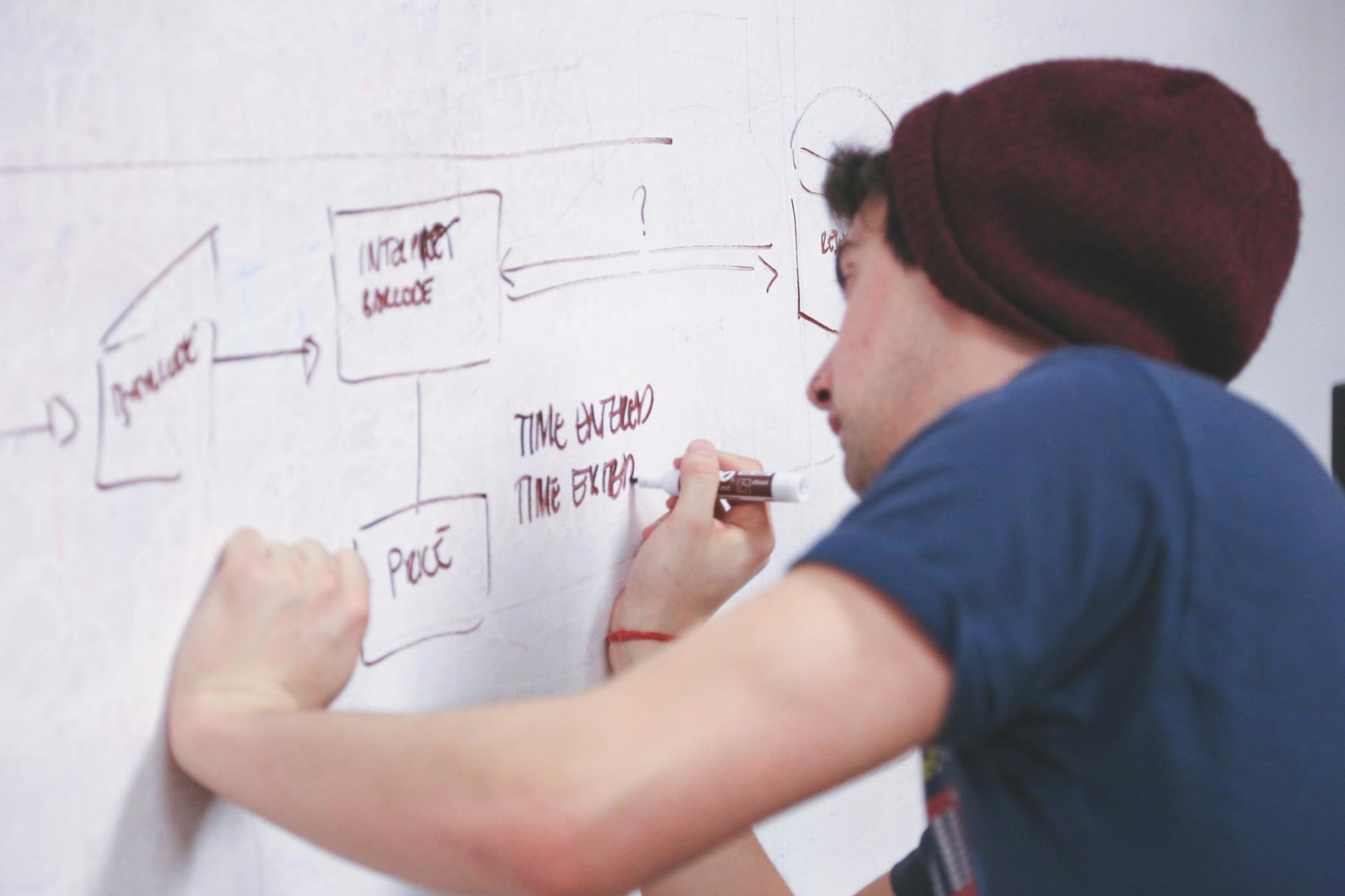
In today's fast-paced market, streamlining your production process is crucial for maintaining a competitive edge. This article delves into practical strategies to eliminate bottlenecks and boost efficiency. Readers can expect insights on identifying bottlenecks, analyzing workflow, implementing automation, optimizing resource allocation, and fostering continuous improvement and monitoring. By addressing these key areas, you'll be well-equipped to enhance your production process and achieve optimal performance.
Identifying Bottlenecks
Streamlining your production process involves a thorough examination of where delays and inefficiencies occur. Bottlenecks, which are capacity constraints that create backlogs, can significantly hinder your workflow. To effectively identify these bottlenecks, consider the following questions:
- What are the factors contributing to the bottleneck, and are these factors related to people, systems, or organizational structures?
- Does the bottleneck occur around handoffs among multiple groups?
- Is the bottleneck the result of an internal or external constraint? What is the nature of the constraint—resource availability or rules?
Analyzing these aspects can uncover unnecessary motion, waiting time, and transportation steps, which add no value to the process. For instance, when the process accelerates or slows, observe what happens to downstream processes. This type of analysis can reveal disconnections and inefficiencies that need to be addressed.
Minimizing handoffs and ensuring that each action adds value to the process are crucial steps. Managing data or product inputs close to the source can also help in reducing delays. A pragmatic review of the current best practices from all process variations currently in use can drive process efficiency and effectiveness. Designing process controls and guidance ensures the execution of best practices, reducing or eliminating variations, exceptions, and errors.
For companies looking to document and automate their business processes, tools like HEFLO can be invaluable. By leveraging such tools, you can gain a clearer understanding of your workflow and identify bottlenecks more effectively.
Watch our latest video on business process automation and discover how to transform your organization for maximum efficiency. Don't miss out – your path to better business starts here!
Analyzing Workflow
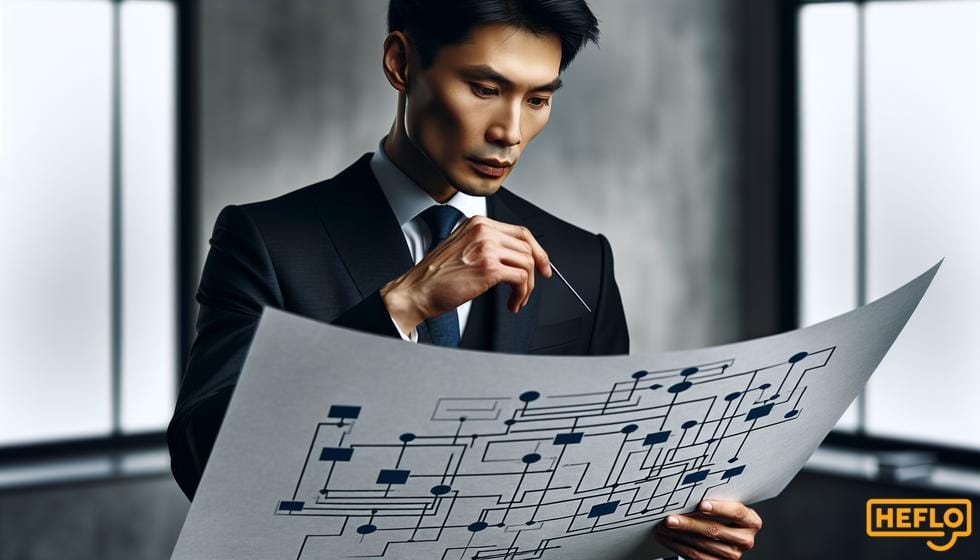
To streamline your production process and eliminate bottlenecks, a thorough analysis of your workflow is essential. This involves examining each step of the process to identify areas where inefficiencies occur. The focus should be on reducing extra motion, waiting time, and transportation steps, which can add value as the work is redesigned. This type of analysis can uncover unnecessary motion for material-related bottlenecks and disconnections.
If the bottlenecks are related to staffing or organizational structure, changes will depend on the organization's ability to manage human resource issues. One commonly overlooked analytical component is the examination of the human motivational and reward systems in place for the process. The reward system could include various incentives such as job structure, promotional opportunities for mastering additional skill sets and competencies, bonuses, and emotional satisfaction. Understanding these motivations and rewards when a process is analyzed will help uncover unseen disconnects and bottlenecks in the process.
Further, the motivation and reward analysis should also consider what rewards should be in place to positively affect any new process or activity that is introduced. This may include minimizing handoffs, ensuring that each action adds value to the process, and managing data or product inputs close to the source. To deliver significant improvement to the organization with very low risk, the team should review the process to ensure that all participants accurately execute the same best practice.
The team can drive process efficiency and effectiveness through a pragmatic review of the current best practice from all process variations currently in use. Then, it can design process controls and guidance to ensure execution of the best practice and reduce or eliminate variations, exceptions, and errors.
Unlock the secrets of workflow analysis with this exclusive YouTube video—don't miss out!
Implementing Automation
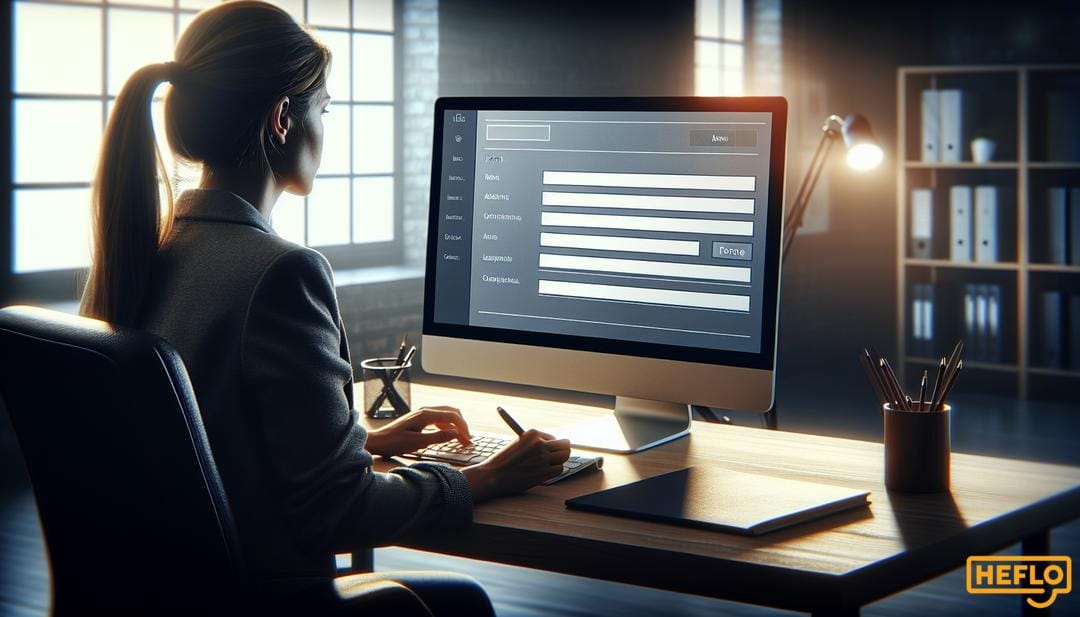
In the quest to streamline production processes and eliminate bottlenecks, automation plays a pivotal role. By automating repetitive and voluminous tasks, companies can significantly reduce the time and effort required to complete these activities, thereby boosting overall efficiency.
Automation applied to an efficient operation will magnify the efficiency. Automation applied to an inefficient operation will magnify the inefficiency. - Bill Gates
One of the first steps in implementing automation is to redesign the process. Before considering automation, it's essential to evaluate and optimize the existing workflow. This involves creating a single point of contact for the customer, combining processes around clusters, and reducing handoffs. By minimizing the number of handoffs, the process becomes more streamlined and less prone to delays.
Another critical aspect is to reduce batch sizes. Smaller batches can move through the production process more quickly, reducing waiting times and transportation steps. This not only speeds up the process but also helps in identifying and addressing bottlenecks more effectively.
Access to information is another area where automation can make a significant impact. By putting access to information where it is needed the most and capturing information once to share it with everyone, companies can ensure that all participants are on the same page. This reduces errors and variations, leading to a more efficient process.
Designing for desired performance metrics is also crucial. By defining the activities, rules, and handoffs of the new process, companies can set clear expectations and standards. This helps in monitoring and measuring the performance of the automated process, ensuring that it meets the desired efficiency and effectiveness goals.
Standardizing processes and considering co-located networked teams and outsourcing are additional strategies that can complement automation efforts. By ensuring that all participants accurately execute the same best practice, companies can drive process efficiency and effectiveness.
Optimizing Resource Allocation
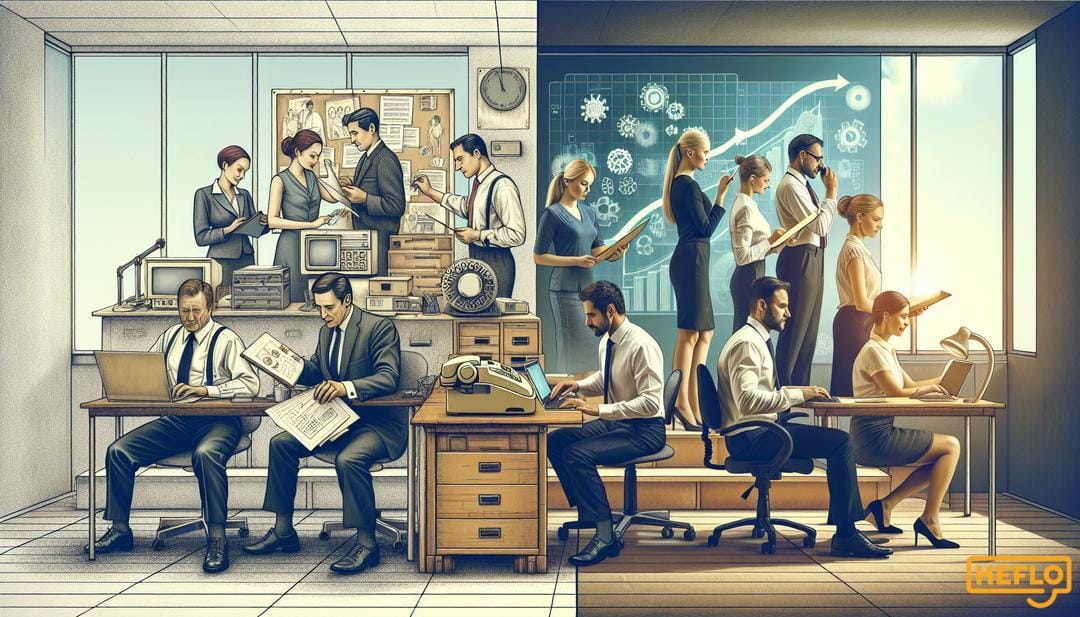
Efficient resource allocation is a key component in streamlining your production process. By strategically distributing resources, you can significantly reduce extra motion, waiting time, and transportation steps, which are often the culprits behind production bottlenecks. This type of analysis can uncover unnecessary motion for material-related bottlenecks and disconnections, leading to a more fluid and efficient workflow.
One effective method for optimizing resource allocation is to conduct a thorough analysis of your current processes. Identify areas where resources are either underutilized or overburdened. For instance, if a particular machine is frequently idle while another is constantly in use, it may be beneficial to redistribute tasks or invest in additional equipment to balance the load.
Another approach is to implement a just-in-time (JIT) inventory system. This strategy ensures that materials and components are delivered exactly when they are needed, reducing the need for excessive storage and minimizing waiting times. By aligning your inventory levels with your production schedule, you can free up valuable resources and space, allowing for a more streamlined operation.
Additionally, consider leveraging technology to enhance resource allocation. Advanced software solutions can provide real-time data and analytics, helping you make informed decisions about where to allocate resources most effectively. These tools can also automate routine tasks, freeing up human resources for more complex and value-added activities.
Regularly reviewing and adjusting your resource allocation strategy is also essential. As your production demands change, so too should your allocation of resources. Periodic assessments can help you stay ahead of potential bottlenecks and ensure that your production process remains as efficient as possible.
What is just-in-time (JIT) inventory system? Learn more about it with this exclusive YouTube video we’ve handpicked just for you. Don’t miss out!
Continuous Improvement and Monitoring
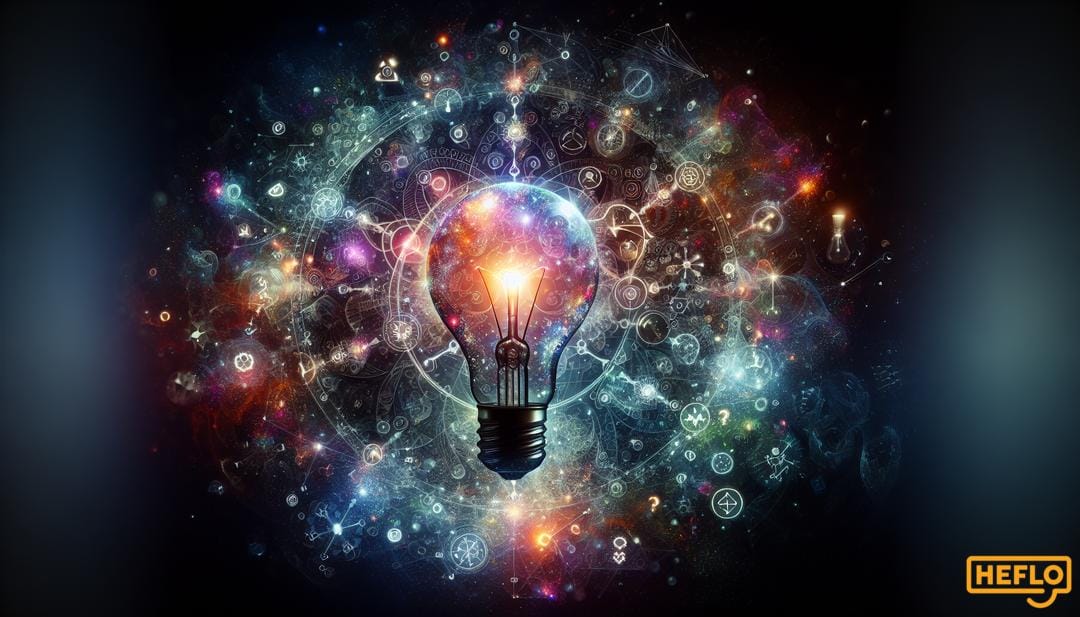
To streamline your production process and eliminate bottlenecks, it is essential to adopt a mindset of continuous improvement and monitoring. This approach involves regularly reviewing operations to identify problems, opportunities for cost reduction, and areas for streamlining. By doing so, you can optimize your processes and enhance overall efficiency.
Continuous improvement is often associated with process methodologies that provide ongoing insight, measurement, and feedback on process performance. Techniques like Six Sigma can be employed to identify, define, measure, analyze, improve, and control business processes. This leads to a continuous list of improvement opportunities and related projects, allowing the company to optimize its operations.
Effective monitoring is a critical component of continuous improvement. Business Process Management (BPM) should include real-time monitoring tools to evaluate processes as they are performed. When deviations in process performance arise, ongoing process analysis allows for timely corrective actions or new analysis towards process change. This ensures that the processes meet the identified goals of the organization.
Several events can trigger process analysis, including strategic planning, performance issues, and the introduction of new technologies. For instance, updates to the strategic plan may necessitate changes in processes to align with new organizational goals. Similarly, performance issues such as unacceptable product quality or deviations from regulatory requirements can prompt a review of the processes to identify and address the root causes.
Advances in technology can also impact process performance, either positively or negatively. As part of implementation or upgrade planning, process analysis helps in understanding how new technologies should be applied to gain maximum benefit and what their impact will be on other processes. This ensures that increased workflow can be managed seamlessly and uniformly across different channels.
By continuously monitoring and improving processes, organizations can ensure that they remain efficient and effective in meeting their goals. This approach not only helps in eliminating bottlenecks but also in boosting overall productivity and efficiency.
In conclusion, streamlining your production process is essential for eliminating bottlenecks and boosting overall efficiency. By identifying and addressing the root causes of these bottlenecks, you can ensure a smoother workflow, reduce downtime, and increase productivity. Implementing strategies such as process automation, regular maintenance, and continuous improvement can significantly enhance your production capabilities. Ultimately, a well-optimized production process not only saves time and resources but also positions your business for long-term success in a competitive market.